Do-It-Yourself EHS MIS
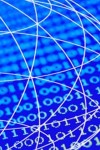
The Green Tie: Why did you decide to build your own system?
We originally had a system that was an off-the-shelf system and it became very cumbersome and labor intensive. We took the best attributes and decided to take a home-grown approach.
The Green Tie: What do you like about your new proprietary system?
One of the things we didn’t have with our old system was the ability to instantaneously enter data. To address that, the IT designers developed an incident reporting system that allows the site user to enter an event right away. (We own power plants across the world so when something happens, we all want to know about it quickly.) That event is then instantaneously sent to a selected group of people within our company through our internal e-mail system, with a timeframe based on the severity of the incident.
In the health and safety area, for example, a lost time incident needs to be entered within that shift, but whereas an unsafe act or condition could be entered by the end of the week. So we try to prioritize incidents and act on them based on that priority. It also allows us to make a comment back or an email back to check in and find out what’s going on. So it really makes our job easier on the incident side.
The Green Tie: Before you created your ‘BITS’ system, InterGen used multiple tracking systems. What are some of the benefits associated with streamlining your efforts?
The operations team, the maintenance team and the HSE teams work very closely together, so the new system allows us to enter incidents related to equipment, health and safety environment and even now, security. The plant teams can use this one system to add an event, to search an event, to look at monthly data, to look at reports, all in one screen.
Often times if there’s an equipment failure, it might have health safety or environmental implications. If you have a machine that uses oil and that machine fails, for example, you might have a spill around the equipment. With this system, you can track that both ways. All this then rolls up in a monthly report that we can generate based on location or by the fleet for everything going on in the company.
The Green Tie: Has the system changed your safety culture? If so, how?
I think the culture is changing based on the fact that people are now very comfortable reporting all incidents. For the past several years, we have emphasized that we need to collect data to track it because the more data we have, the better off we’ll be.
The new system encourages reporting system and makes it easier for us to trend data. People love to report things now but they expect us to report back to them with the results. So we provide feedback via trending on a quarterly basis and we develop programs, procedures and processes based on the trends that we see.
We can now track incidents by body parts, for example. If we see a bunch of eye injuries, we’ll be able to investigate that issue and look at whether our safety glasses program is working. And all the coordinators on the site-level appreciate it that we’re looking at it from a corporate or fleet approach and offering recommendations on how to address these issues.
The Green Tie: What were some of the challenges of putting a system like this together?
The first thing is internal cost. After that, it’s a matter of getting employees focused, making it a priority, and keeping up with it. And we found that if you don’t keep up with it, it’s not going to work. Every year, we do a survey of users to ask them what else they’d like us to track. We then issue an update once a year.
Teaching employees how to use it is another consideration. We’ve learned that if you don’t do the proper level of training, people are not going to use it. So we have a full-time IT/training coordinator and we work together on each year’s release. We have video conferencing with everybody; and we have a test site they can try out before it goes live. All these things are important to get people comfortable with it.
The Green Tie: If you could do it again, what are some of the things you would do differently?
What I think we learned is if you spend more time in the design phase it will save you time with the updates. We have far fewer changes this year than last year, but I think it’s important take a lot of time to chart out the plan. Getting more people involved also could have helped make the process smoother. Often times people who are unfamiliar with the issue can help catch things you overlook.
To learn more about InterGen’s internally built system or to discuss the latest trends in management information systems (MIS), join NAEM in San Antonio March 2 and 3 for the 2011 EHS MIS Conference.
Topics:
Health & Safety Metrics & Reporting
About the Author
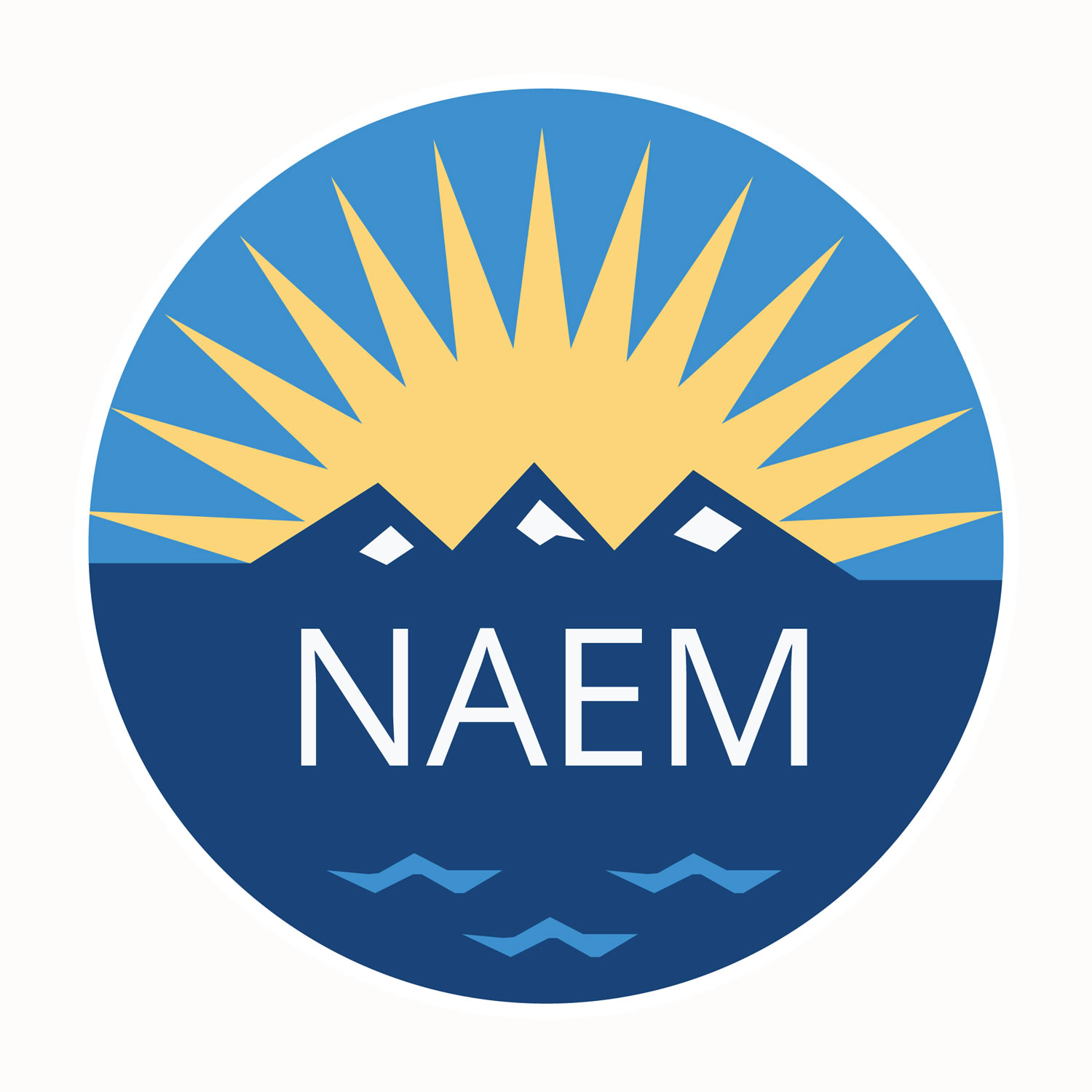
NAEM Staff
The National Association for Environmental, Health and Safety, and Sustainability (EHS&S) Management (NAEM) empowers corporate leaders to advance environmental stewardship, create safe and healthy workplaces and promote global sustainability. As the
leading business community for EHS&S decision-makers, we provide engaging forums, a curated network, peer benchmarking, research insights and tools for solving today’s corporate EHS&S management challenges. Visit us online at naem.org.