Interface Inc.'s 'Mission Zero' Journey
In 1994, Ray Anderson, founder of Interface, Inc., outlined an ambitious new vision for his company: to achieve sustainability by 2020. Lindsay Stoda, a Senior Business Analyst with the company, spoke at the recent EHS Management Forum about the metrics Interface uses to measure its sustainability progress. This week, we caught up with Lindsay to learn more about the company’s Mission Zero goals.
Lindsay Stoda
Q: Where did the Mission Zero goal come from?
LS: Sparked by questions from customers and the ideas he encountered in Paul Hawken’s book, “The Ecology of Commerce,” our founder Ray Anderson realized that business and industry were part of the larger system that was damaging the environment and that it was not going to be a sustainable future if business continued in that direction. And realizing that it was someone’s job to lead industry down that path, he decided to ask his company and his employees to be that leader.
Q: How do you measure success against your Mission Zero Goals?
LS: We’ve always followed the “What gets measured gets managed” philosophy, so our way of being able to track and ensure that we’re making progress is through four different measurement platforms:
Q: How did Mission Zero change the work of Interface’s EHS department?
LS: Prior to Ray’s epiphany, we had a more traditional manufacturing environment, health and safety (EHS) department focusing on safety and compliance. Today, it’s typically the same folks because the tracking of that kind of information all kind of overlaps with the sustainability roles, except that people’s EHS roles developed a sustainability-minded focus.
Q: Can you tell me about some of your efforts toward creating closed loop products?
LS: We have a strong push to create closed loop products using recycled and bio-based raw materials. This process basically involves returning the materials in used finished product back to raw materials.
For carpet tile, there are two main components: There’s the face fiber and the fluff -- the surface that you walk on -- and then there’s the backing, which is different from residential carpet in that it’s a vinyl backing and it’s heavier, to hold the tiles to the floor and give them dimensional stability.
We had previously been able to cut the fibers off the front, take the backing, crumble it up, melt it down and return it to backing. But now we’re able to take the nylon fibers from the face of the products, shave them off and return them to our fiber suppliers to create new face fiber with post consumer recycled content.
We bring back both our carpet as well as competitors’ products through ‘ReEntry’—our recycling program. We collect used product back from the marketplace, run it through our process, and return backing to backing and fiber to fiber. Since the program began, we have diverted more than 100,000 tons of material from landfills.
Q: One of the goals you’ve identified is providing Environmental Product Declarations (EPDs) for all of your InterfaceFLOR products by 2012. What does that entail?
LS: We have used life cycle assessment (LCA) for several years now as we’ve tried to evaluate different materials and processes for manufacturing our products. The Environmental Product Declaration is a 10-15 page summary of the life cycle assessment results, everything from global warming potential to toxicity to resource use throughout the entire life cycle of the product. There is a lot of different environmental information out there and we thought the most useful thing for our customers would just be to give them the facts they need to make the decisions about what type of products they’d like to purchase. So it’s really the good and the bad. It’s just the facts. We collect the data and have it third-party verified to ensure it is complete and accurate.
You can hear Lindsay talk more about using metrics during “Defining the Metrics that Matter,” part of NAEM’s Best of the 2010 Forum webinar series, on Tuesday, Nov. 16. To register, visit www.naem.org.

Q: Where did the Mission Zero goal come from?
LS: Sparked by questions from customers and the ideas he encountered in Paul Hawken’s book, “The Ecology of Commerce,” our founder Ray Anderson realized that business and industry were part of the larger system that was damaging the environment and that it was not going to be a sustainable future if business continued in that direction. And realizing that it was someone’s job to lead industry down that path, he decided to ask his company and his employees to be that leader.
Q: How do you measure success against your Mission Zero Goals?
LS: We’ve always followed the “What gets measured gets managed” philosophy, so our way of being able to track and ensure that we’re making progress is through four different measurement platforms:
- Eco Metrics: Measure environmental impact
- Socio Metrics: Measure social impacts
- Quest program: Measures waste elimination
- Ecosense: Measures the activities on a plant-level that contribute to our sustainability goals
Q: How did Mission Zero change the work of Interface’s EHS department?
LS: Prior to Ray’s epiphany, we had a more traditional manufacturing environment, health and safety (EHS) department focusing on safety and compliance. Today, it’s typically the same folks because the tracking of that kind of information all kind of overlaps with the sustainability roles, except that people’s EHS roles developed a sustainability-minded focus.
Q: Can you tell me about some of your efforts toward creating closed loop products?
LS: We have a strong push to create closed loop products using recycled and bio-based raw materials. This process basically involves returning the materials in used finished product back to raw materials.
For carpet tile, there are two main components: There’s the face fiber and the fluff -- the surface that you walk on -- and then there’s the backing, which is different from residential carpet in that it’s a vinyl backing and it’s heavier, to hold the tiles to the floor and give them dimensional stability.
We had previously been able to cut the fibers off the front, take the backing, crumble it up, melt it down and return it to backing. But now we’re able to take the nylon fibers from the face of the products, shave them off and return them to our fiber suppliers to create new face fiber with post consumer recycled content.
We bring back both our carpet as well as competitors’ products through ‘ReEntry’—our recycling program. We collect used product back from the marketplace, run it through our process, and return backing to backing and fiber to fiber. Since the program began, we have diverted more than 100,000 tons of material from landfills.
Q: One of the goals you’ve identified is providing Environmental Product Declarations (EPDs) for all of your InterfaceFLOR products by 2012. What does that entail?
LS: We have used life cycle assessment (LCA) for several years now as we’ve tried to evaluate different materials and processes for manufacturing our products. The Environmental Product Declaration is a 10-15 page summary of the life cycle assessment results, everything from global warming potential to toxicity to resource use throughout the entire life cycle of the product. There is a lot of different environmental information out there and we thought the most useful thing for our customers would just be to give them the facts they need to make the decisions about what type of products they’d like to purchase. So it’s really the good and the bad. It’s just the facts. We collect the data and have it third-party verified to ensure it is complete and accurate.
You can hear Lindsay talk more about using metrics during “Defining the Metrics that Matter,” part of NAEM’s Best of the 2010 Forum webinar series, on Tuesday, Nov. 16. To register, visit www.naem.org.
Related
About the Author
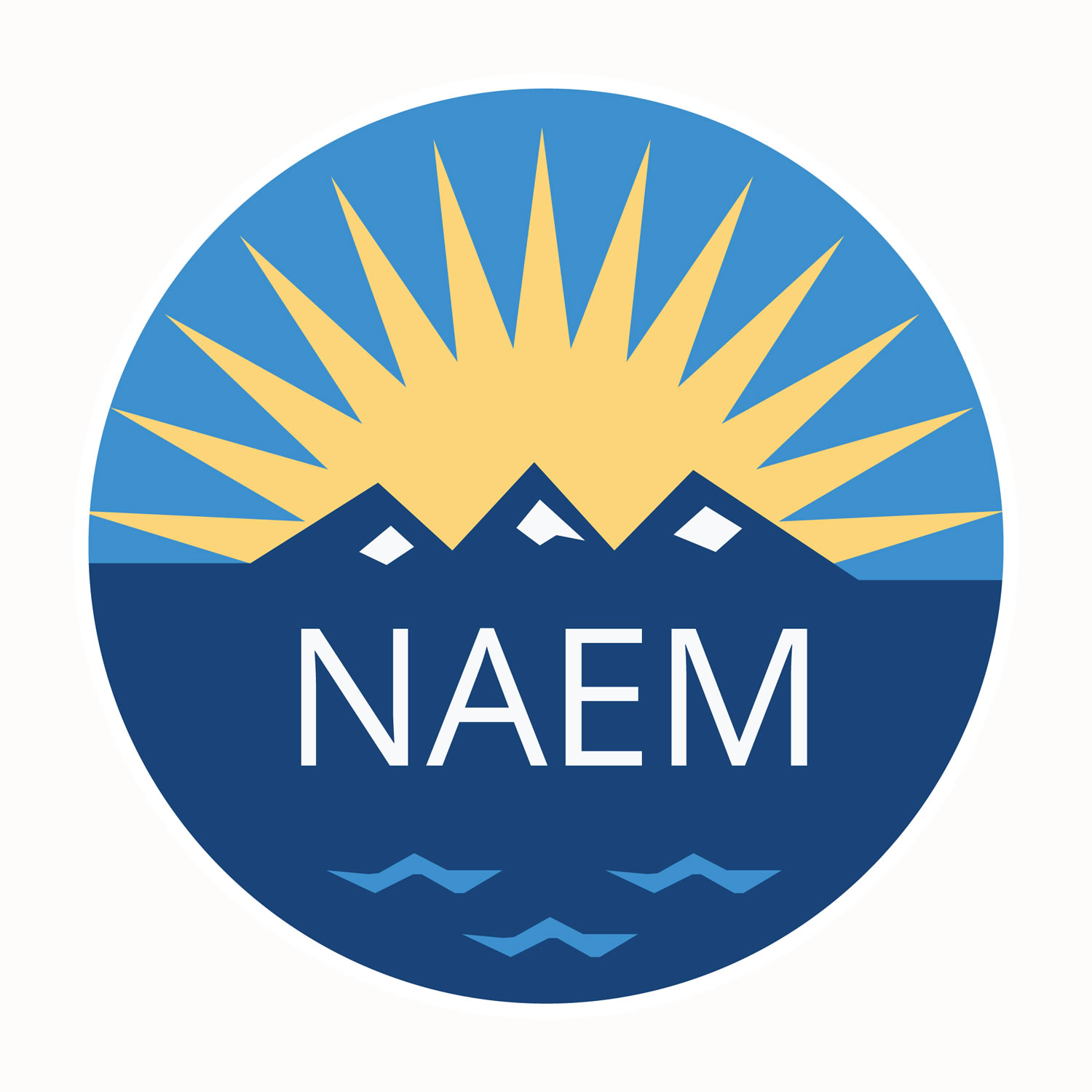
NAEM Staff
The National Association for Environmental, Health and Safety, and Sustainability (EHS&S) Management (NAEM) empowers corporate leaders to advance environmental stewardship, create safe and healthy workplaces and promote global sustainability. As the
leading business community for EHS&S decision-makers, we provide engaging forums, a curated network, peer benchmarking, research insights and tools for solving today’s corporate EHS&S management challenges. Visit us online at naem.org.