Setting the Sights on Forward-Looking Metrics
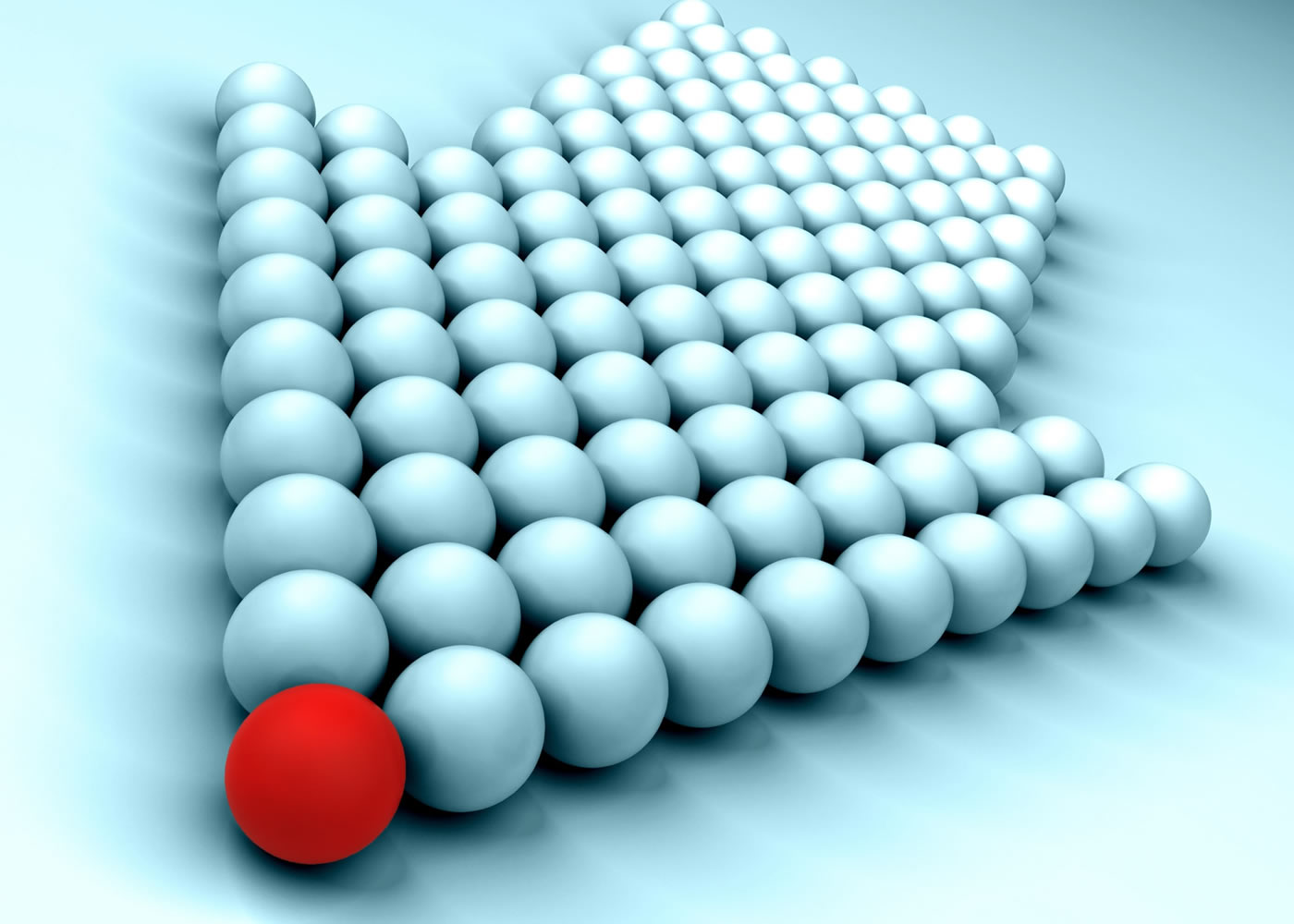
"Lagging indicators are like driving a car while looking in the rearview mirror," he said.
For years, U.S. companies have reported their EHS metrics using the criteria required by the Occupational Safety and Health Administration (OSHA). By the time these numbers are compiled by the Bureau of Labor Statistics, though, Mr. Rosenblum says they are already outdated.
"Imagine a bank analyzing its financial situation by looking at two-year old interest rates, or businesses looking at their sales from two years ago and saying, ‘What's the next hot thing we need to stock our shelves with this year?'" he said.
"No other part of business functions this way. Only safety."
The solution, Mr. Rosenblum says, lies in developing forward-looking tools that reflect current activities and can actually help EHS leaders prevent incidents before they occur.
One of those tools are leading indicators.
Michelle Garner-Janna, Director of Corporate Health and Safety at Cummins Inc., said her team first started thinking about leading indicators when the company's recordable incident rates fell to statistical lows.
"Once you get to the 1.0 incident-level, things get a lot more difficult from a metrics standpoint," she said. "It gets exponentially harder to move the needle."
Her team had read about the use of leading indicators in professional journals and thought they could be a good strategy for encouraging the kinds of behaviors that reduce risks.
"We wanted to be a little more proactive," she recalled. "We also wanted to be able to engage as many employees and we could in the process and be able to measure that engagement."
In search of the perfect metrics, they conducted literature reviews, benchmarked with other companies and talked to researchers. The result?
"We eventually realized that there wasn't going to be an ideal one or two or three," Ms. Garner-Janna said. "We had to choose the ones that we thought would have the most impact for us."
In the first year, the company simply picked two metrics and launched a pilot program.
"Those were two that were easy to get to, it didn't require a lot of burden on the sites, but the problem was that it didn't really tell us much," she said. "It gave us an idea of whether or not we were making improvements, but it didn't necessarily give us strong correlation with our lagging indicators."
Still, the team was undeterred. Based on the insights from the first year, they added four additional indicators and tracked the data anew. When the team conducted a correlation analysis of those results, Ms. Garner-Janna says she was surprised at what she found.
"One of them in particular, had by far the highest correlation with incident rates. And that happened to be training hours," she said.
Upon investigation, she discovered that the training emphasized a ‘find-it, fix-it' approach, which taught employees how to reduce risks in the workplace. A strong safety culture at the site-level in turn contributed to reduced workplace incidents. The company then used that insight to set new targets for training, which had not previously been part of its performance goals.
"That was really eye-opening for us," Ms. Garner- Janna said. "We were in the dark until we had that information in front of us. And then once we had that evaluation, it was really easy to see: ‘Ok, this is where we need to focus.'"
This thoughtful approach to experimentation is likewise how Toyota Motor Sales develops the forward-looking EHS metrics it uses to keep its eyes on the horizon, according to Ryan McMullan, Environmental, HazMat & Safety Programs Administrator.
As part of its five-year strategic planning cycle, Toyota's EHS team develops what it calls ‘strategic indicators,' a set of targets that support the company's long-term goals.
Similar to leading indicators, strategic indicators are specific to each business and even to a particular business goal. As such, no one size fits all, Mr. McMullan says. Unlike leading indicators, strategic indicators are less predictive than prescriptive.
"It's looking for strategic direction," he said. "Given that we want to be an environmental role model in 2021, how do we need to think about the topics differently? And backing into how do we need to measure them differently?"
One example of how Toyota uses strategic indicators is in advancing its waste management program. When the company was focused on increasing its recycled waste from 30 to 90 percent, a recycling rate metric was a useful measure to track, Mr. McMullan said. Once recycling approached the 90 percent mark, however, the metric stopped accurately reflecting progress.
"We started encountering cases where if we reduced a waste that we used to recycle, we're taking it out of the recycling bin and our recycling rate went down," he said. "We know that reduced [waste] is better than [recycled] waste, but our indicator was saying, ‘No, put that back in the recycling bin because we need it there.'"
Coming up with a new metric to replace recycling rate, though, required a few tries.
"That's where we started to do what I call ‘kissing frogs' and in a spreadsheet trying out a whole bunch of different metrics [while] trying to be mindful of ‘What data do we have now, what data could we get without requiring too much burden on the business unit?'" he said.
Mr. McMullan's team also ran a number of scenarios to see if the indicator accurately aligned what they knew actual progress looked like. In other words, one that would show them that recycling is good, but reducing waste is better.
"We tried to pick the indicator that gave us the ‘right' compass reading for our conceptual understanding of the issue," he said.
Going beyond lagging indicators is a one part art, the other part science, though, Mr. McMullan says.
"A lot of this is uncharted territory. We can't just go and copy some other company and say, ‘Oh well, here's the easy roadmap," he said.
Ms. Garner-Janna agrees that the uncertainty associated with creating new, forward-looking metrics requires a more creative approach to data collection.
"That's probably why a lot of companies are struggling a little bit on the leading indicator side because there's not a template or a format or ‘Here are your instructions for implementing leading indicators,'" she said.
To be done correctly, she says each company needs to focus on its unique EHS challenges.
"If you really want to have indicators that are effective, and that will drive down your lagging indicators, then it's really important that they be tailor-made and customized to what your individual issues are," she said.
The same holds true for strategic indicators, Mr. McMullan says.
"It's really tempting to say, ‘We're going to tackle every environmental issue now," he said. "I think a much better way of starting is to say, ‘What's one to maybe three of the most important issues to our company? Where do we want to have the biggest impact? Where can we make the highest benefit? And just focus on understanding those first."
And no matter where you start the metrics development journey, Ms. Garner-Janna says, it's important to continue refreshing those indicators over time.
"What's working today may not necessarily work tomorrow. You've got to really stay on top of that and continually evaluate the process," she said.
After all, no one number will answer all the questions, she says.
"Had we understood that there is no holy grail of leading indicators in the beginning, we could have saved a lot of time," she said.
Topics:
Metrics & Reporting
Related
About the Author
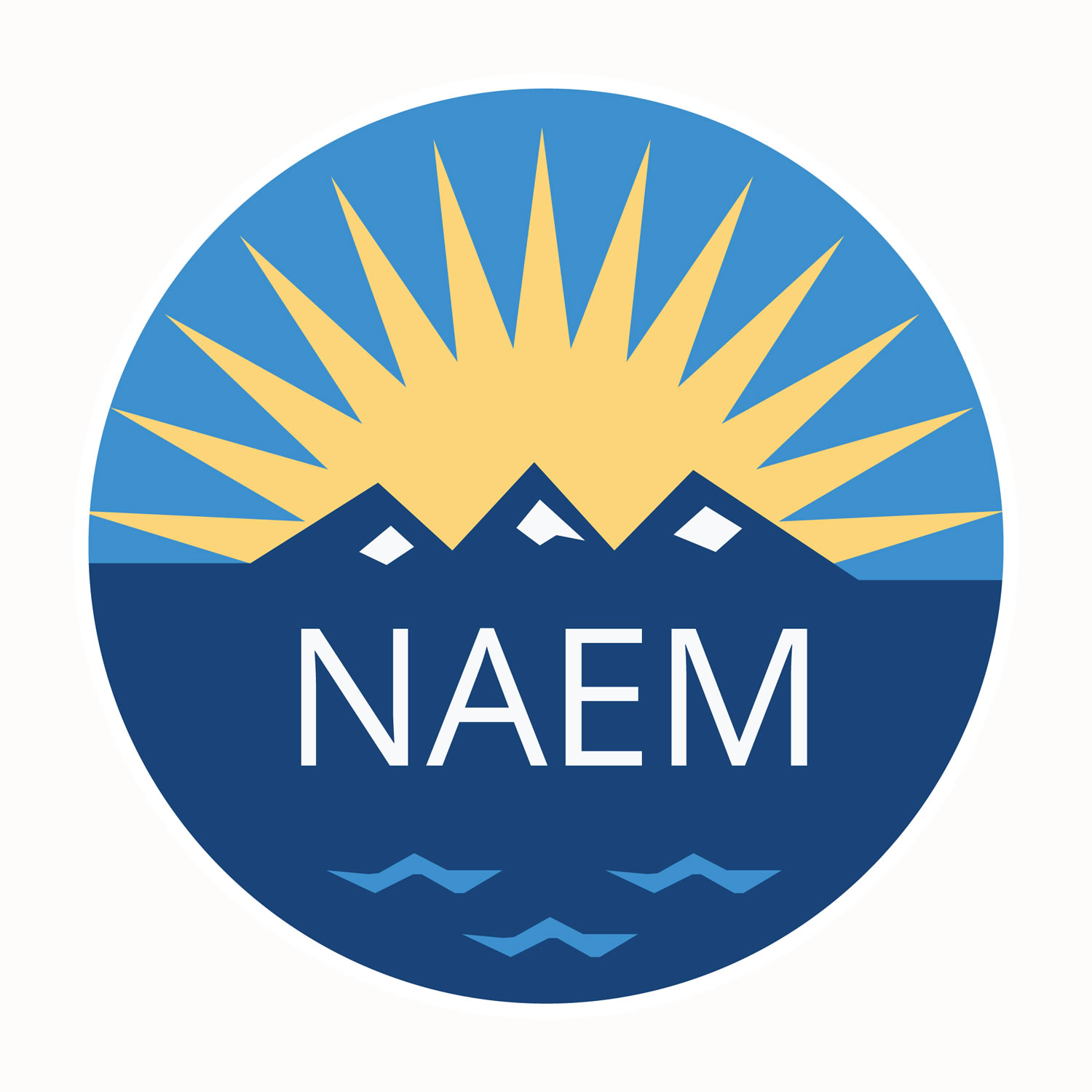
NAEM Staff
The National Association for Environmental, Health and Safety, and Sustainability (EHS&S) Management (NAEM) empowers corporate leaders to advance environmental stewardship, create safe and healthy workplaces and promote global sustainability. As the
leading business community for EHS&S decision-makers, we provide engaging forums, a curated network, peer benchmarking, research insights and tools for solving today’s corporate EHS&S management challenges. Visit us online at naem.org.