Understanding OSHA's Globally Harmonized Hazard Communication Standard
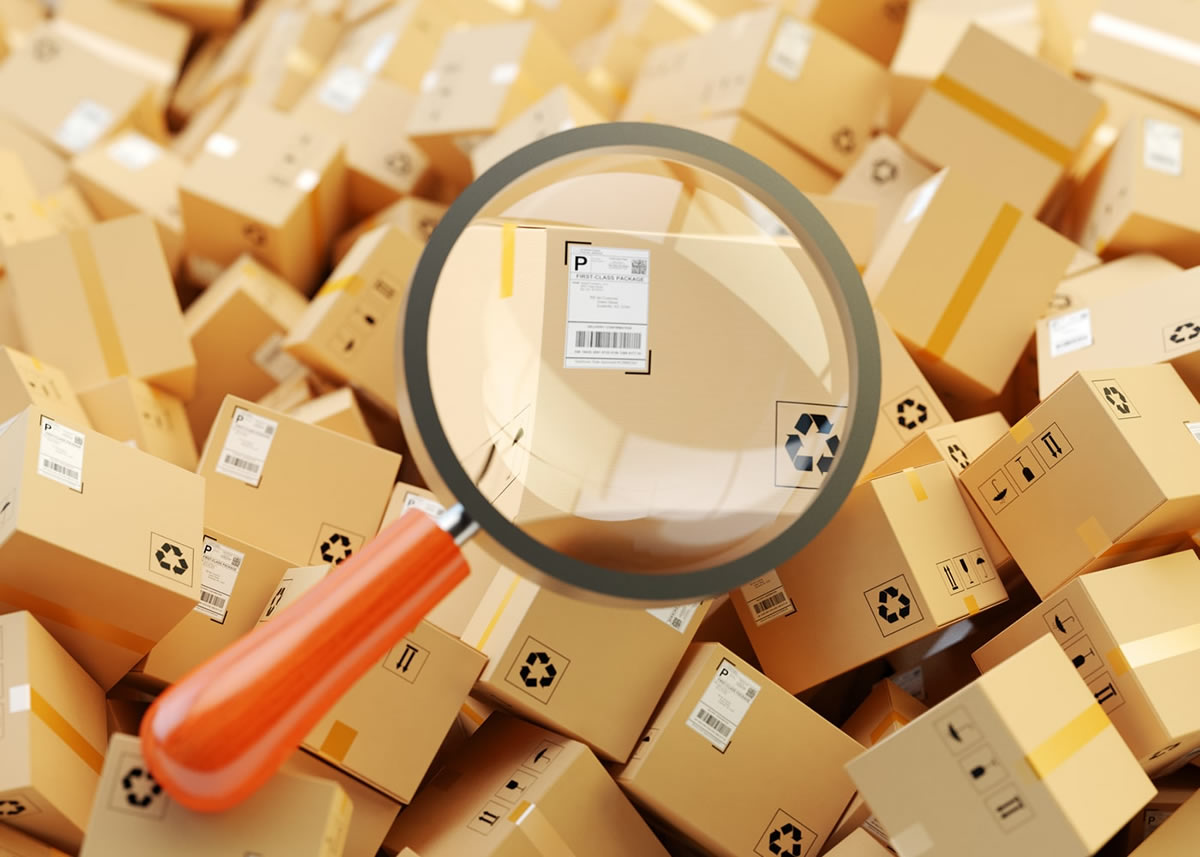
NAEM: What's the genesis of this latest HCS update?
MD: OSHA adopted the HCS in 1983 and since then they've made a number of adjustments to it. They made the latest round of changes for two reasons. The first is because the GHS is out there and the United States wants to harmonize its hazardous communications with those of other countries for the promotion of international trade. The second is that the agency believed that GHS would represent a clear improvement in the hazardous communication standard and thus help protect employee safety.
NAEM: What is the GHS?
MD: In 1992 the United Nations Conference on Environment and Development issued a mandate to develop a globally harmonized chemical classification and labeling system. It adopted the GHS in 2003. The standard was intended to create a common system for hazard communications. At the time, the lack of consistency across countries was a burden to international trade.
The GHS applies to hazardous chemicals. It doesn't apply to articles, or products that have a fixed shape, which are not intended to release a chemical. There are also exemptions for certain kinds of chemicals that are subject to detailed regulation in specialized areas. So drugs, toy additives and pesticide residues in food 'at the point of intake' are not covered by GHS. It does, however, apply to worker exposure and transportation of drugs, food additives and pesticide residues in food.
It's important to note that the GHS is a hazard-based system designed for trade; it's not a risk-based system. Each company in the supply chain must consider its own risk and exposure conditions and decide on risk abatement measures.
NAEM: How does OSHA's rule compare to the GHS?
MD: Let's begin by talking about the three main elements to the GHS:
1. The classification system: The GHS has identified physical hazards, chemical hazards and environmental hazards, and classified them by defining them and defining different categories within each hazard class with objective criteria. Once a classification for a chemical component has been determined, you then need to classify the mixture to which it belongs. Under the old OSHA standard, there was a pretty simple rule for determining the hazards of a mixture. The mixture was determined to have all the health hazards present if they had it at .1 percent or greater, with no regard to dilution. And that ran into a problem with acute toxicity for example if you took something that was acutely toxic at 100 percent and dilute it down to 5 percent, it might not qualify as acutely toxic anymore. What GHS does is it provides guidance on how to calculate the hazards of a mixture depending on the particular hazard categories of the various components and their proportions in the mixture. And there are different approaches for different kinds of hazards. It's more complicated, but it's generally regarded as a more accurate system than the old OSHA system.
2. Labeling: Under the GHS there are multiple things that must appear on the label: the product name, the company's name address and phone number, the standardized hazard statement, a pictogram and a precautionary statement. Under the old OSHA standard, you could express a hazard using any statement you wanted. Under GHS, there is a prescribed hazard statement assigned to each hazard category. There's also a requirement for a pictogram, or a symbol conveying a visual idea of the hazard. A precautionary statement is what you should do in response to this hazard information (e.g. first aid instructions, personal protective equipment). And finally, there's a requirement for a signal word. One is 'Danger,' the other is 'Caution'. This is all different from the old OSHA rule, which required only the name and address, the name of the product and "appropriate hazard warnings" (which led to very different descriptions of the hazards for the same product).
3. Safety Data Sheets: A safety data sheet is a written compilation of information about the hazards of that product. In industrial chemicals, there is a list of data elements that have to show up. Under the old OSHA standard there was no required format for that. Now, under GHS and now under OSHA, there's a prescribed format for the disclosure on the safety data sheets. GHS does not use the term 'material safety data sheet', and OSHA is adopting that language so MSDSs will now be called Safety Data Sheets (SDS). There's a standard format and there's also specific information that has to be included in each section.
NAEM: What are some of the differences between the GHS and the updated HCS?
MD: OSHA has not completely taken GHS. There's a whole set of environmental hazards that are classified in GHS, which are not included in the new OSHA rule because the agency doesn't have statutory jurisdiction. However, OSHA does require companies to include the section heading for environmental hazards; the hope is to encourage voluntarily disclosure of that information.
OSHA also adds some requirements that focus on the workplace where chemicals are present and where there is exposure potential. It requires training, it requires a written hazard communication program and it requires labeling of containers and chemicals in the workplace. Because GHS focuses on trade, it doesn't really address the occupational exposure aspect.
The OSHA rule also differs from GHS in its classification requirements. Under the old OSHA standard, you simply had to indicate that something was acutely toxic. Now, under the harmonized rule have to classify the hazard of acute toxicity and put it into one of several buckets. Rather than adopt all five GHS categories, OSHA omitted the lowest toxicity level because it concluded that it wasn't appropriate to in a worker protection context.
NAEM: When does the new OSHA rule go into effect?
MD: The rule goes into effect on May 25, 2012 but compliance will take place in stages:
- Dec. 1, 2013: Deadline for training employees on the new label elements. Companies will start transitioning to GHS and they need to train employees to understand the new label warnings, particularly the pictograms.
- June 1, 2015: Classification, labeling and the SDS requirements. This is the same date that the European version of the GHS goes fully into effect. Distributors, however, may continue to ship products with the old labels until December 1, 2015.
- June 1, 2016: The other workplace requirements take effect. These include requirements for hazard communication program and training on newly identified hazards. Between now and then, companies can comply with old rule, new rule or with both.
About the Author
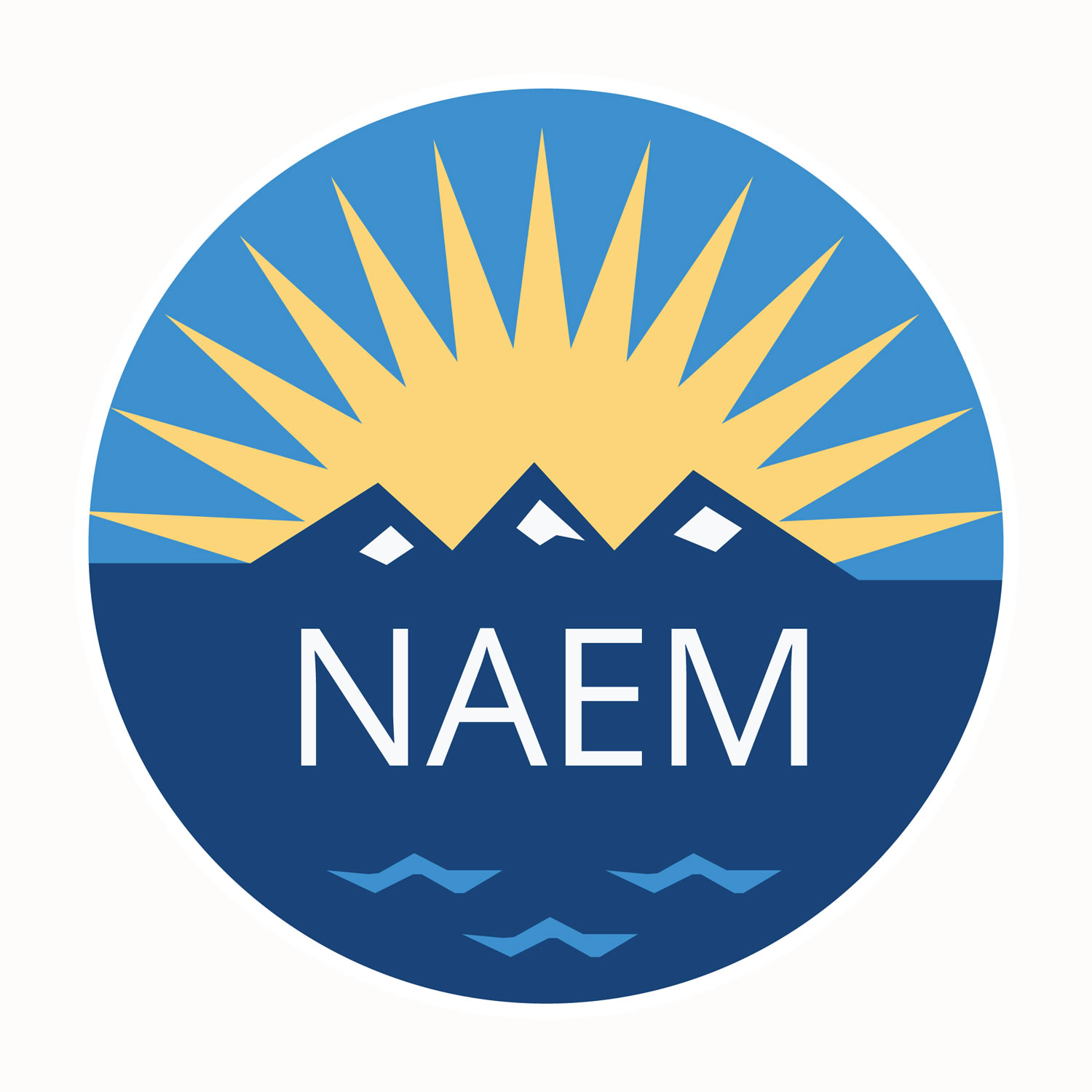
NAEM Staff
The National Association for Environmental, Health and Safety, and Sustainability (EHS&S) Management (NAEM) empowers corporate leaders to advance environmental stewardship, create safe and healthy workplaces and promote global sustainability. As the
leading business community for EHS&S decision-makers, we provide engaging forums, a curated network, peer benchmarking, research insights and tools for solving today’s corporate EHS&S management challenges. Visit us online at naem.org.