Throwing Away the Dumpster: How Burt's Bees Achieved Zero Waste to Landfill
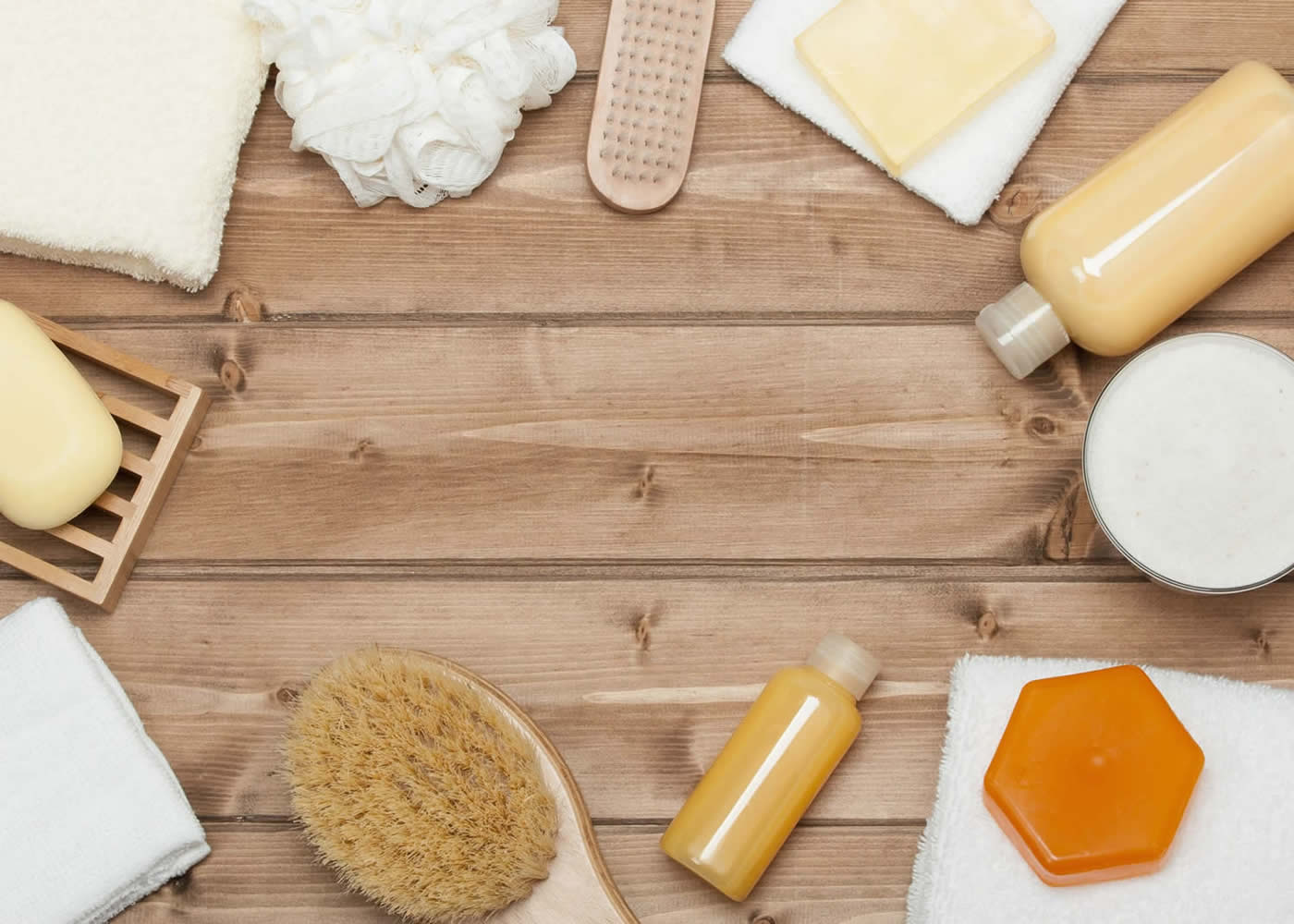
NAEM: How does Burt's define zero waste?
SW: To make our products, there will have to be a certain amount of water and energy use, but we want to be as efficient as we can to ensure that any energy we put in is going directly to adding value to the customer. So when we say zero waste, it's 100 percent efficient in the processes. Our true aim, however, is not only to get to zero, but to have a net-positive impact on the environment and on society.
NAEM: When you started at Burt's, the company had already outlined its zero waste goals. How did you get started?
SW: We began by setting a baseline. We went back and got our water history use, energy use and landfill data, and then starting measuring our by-products. At Burt's, we define 'by-products' as literally everything that leaves one of our buildings other than a person or a finished good. This broad definition runs the gamut from scrap metal to hazardous waste to used batteries to typical recyclables like plastic, cardboard, and paper.
To measure our by-products, we bought industrial floor scales and began weighing everything. The data goes into Excel spreadsheet, which I use to monitor how we are doing by by-product type as a whole, and how are we doing in using our internal by-product hierarchy.
NAEM: What is a by-product hierarchy?
SW: We've established a hierarchy for how we deal with our by-product, ranging from landfilling it (the least preferred method) to reducing it altogether. (The sorting guide has not yet been updated; landfill has now become waste-to-energy.)
NAEM: What were the next steps?
SW: Starting at the bottom of the hierarchy, we worked hard to reduce our waste to landfill. Back in April 2008, we held a Dumpster Day. We took two weeks' worth of trash from our manufacturing and administrative sites, dumped it into the parking lot, and sorted it into three piles: what should have been recycled (material that we already recycled); what could be recycled if we found an outlet for it; and everything else, or the stuff that we needed to eliminate.
We immediately saw an additional 50 percent reduction in waste to landfill as a result of this employee engagement exercise. That drove a cost savings for us, as we reduced our service frequency from weekly, to every other week, to only once per month. That ended for our manufacturing site in October 2009, when our service provider took the trash compactor away for good.
Now there's no going back. It's not like we just put caution tape over the trash compactor and said, "Don't use it." There's no place to throw this stuff out. We have to figure out where we're going to send it other than landfill.
NAEM: The next step in your by-product hierarchy is waste-to-energy conversion. How do you designate which materials belong in that category?
SW: These are the materials that are left over after we've reused, composted or recycled everything that we can. The stream includes break room materials like Styrofoam carry-out trays, potato chip bags, and plastics that aren't numbered. We also have some raw packaging, such as 50-pound bags comprised of plastic and paper. We're continuing to address those through reduction and substitution efforts.
NAEM: How does waste-to-energy work?
SW: Our waste-to-energy story is a little different than most. Many companies that are zero waste to landfill send their materials to a facility that burns them to generate electricity or steam. The problem is, up to 20 percent of what goes in comes out the back end as ash or non-combustibles, which typically still wind up in a landfill.
To avoid this scenario, we work with a waste-to-fuel firm, who takes our materials, shreds them up and blends them with materials from other companies. The resulting fuel has a heat value equivalent to that of coal, which cement manufacturers can use in their process. The real key for me is that the ash from our materials is incorporated into the cement itself - a truly zero landfill process.
NAEM: How does recycling fit into your by-product management process?
SW: An overall challenge with recycling is having enough volume to find a suitable outlet. Because we're a relatively small company, the trick for us is finding others with similar materials so we can put them together and reach the volume necessary to enable the financial side of the equation.
For the past three years we have worked with a professional total by-product management (TBM) firm that does just that. By connecting us with other TBM customers, they're able to deliver the entire volume to their network of recyclers across the country. This allows Burt's Bees to play much larger in the market and affords us additional professional resources to support our TBM efforts without increasing our internal headcount.
NAEM: So is Burt's Bees out of the landfill and incineration categories on the by-product hierarchy altogether?
SW: Yes with respect to landfill. We do continue to generate some waste from our R&D and quality labs that must be incinerated per the U.S. Environmental Protection Agency's rules. The ink and solvents used to put the date codes on many of our products are also regulated. We've minimized the hazardous waste stream to a few hundred pounds per year and continue to explore substitution of other laboratory reagents along with alternate date coding options.
About the Author
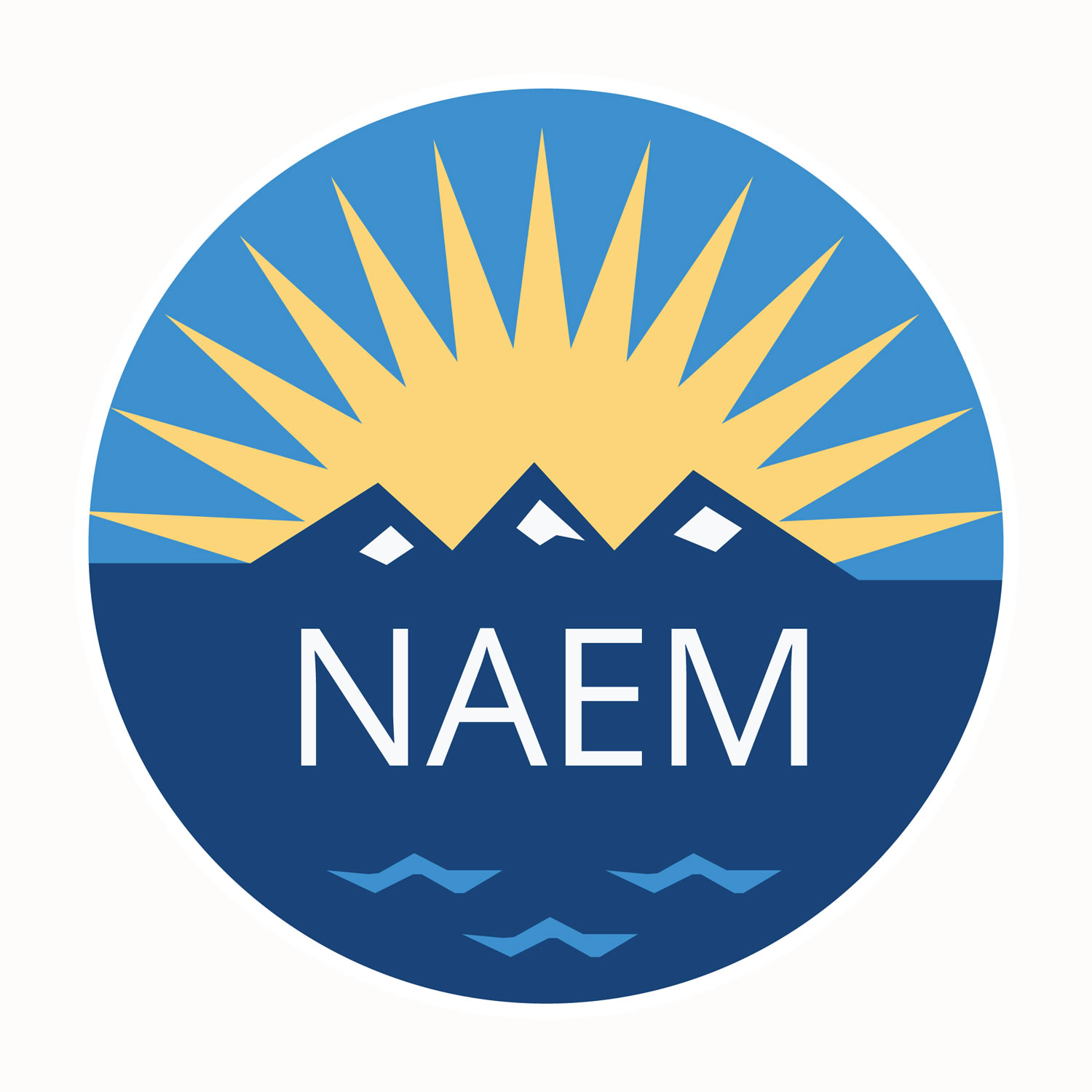
NAEM Staff
The National Association for Environmental, Health and Safety, and Sustainability (EHS&S) Management (NAEM) empowers corporate leaders to advance environmental stewardship, create safe and healthy workplaces and promote global sustainability. As the
leading business community for EHS&S decision-makers, we provide engaging forums, a curated network, peer benchmarking, research insights and tools for solving today’s corporate EHS&S management challenges. Visit us online at naem.org.