Identifying the Sustainability Risks Along Your Supply Chain
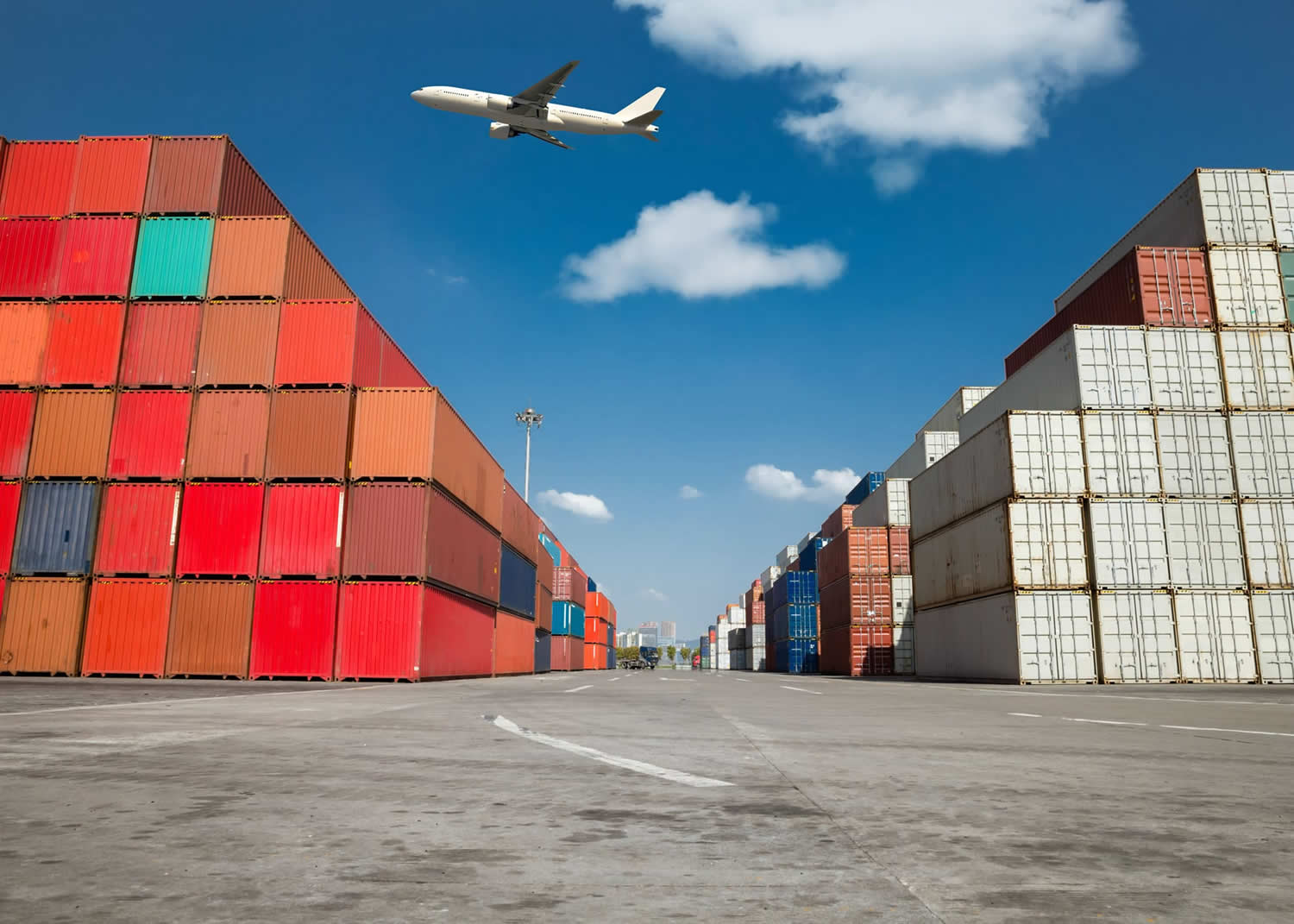
To understand this issue, we spoke with Phil Berry, who has developed corporate social and environmental programs for more than 30 years. During his tenure at Nike, he initiated the company's efforts to green its Asian first-tier factories and raw material suppliers. His team created dramatic reductions in waste, chemical use, water use, and energy use while also making suppliers more profitable. He then helped launch "Nike Considered," which generated significant value for the brand through innovation and customer engagement.
Mr. Berry took a moment to explain the scope of the supply chain challenge and how to eat the elephant one bite at a time.
GT: Why is the supply chain issue so tricky?
PB: Supply chains are not things that EHS and sustainability professionals have traditionally dealt with. It continues to be an issue in the business, but with so many things for EHS or sustainability professionals to look at in their own operations, it’s been hard for them to know where to start. The other challenge is that supply chain professionals don’t really understand sustainability. They’re looking at cost information: cost of labor, cost of goods sold, etc. in terms of this order, this quarter, or next product launch. But they aren’t really looking at the sustainability risks. You’ve got somebody making purchasing decisions, trying to get something five percent cheaper, when the implications for cost reduction may be greater from sustainability issues in the long-term.
GT: What are some of the sustainability risks to the supply chain?
PB: Climate change risk is a good one to look at. For one company I’m familiar with, their issue is that two hurricane-strength storms in the same year would present a serious financial risk. For another company, climate change has had a disruptive impact on their access to commodities, as it has for many companies. In 2012, for example, a major European apparel company missed its quarterly revenue target by 20 percent because it had bet heavily on Pakistani cotton. A climate change-related drought had hit Pakistan, dramatically decreasing the supply and increasing the price. This forced the company to purchase cotton on the higher cost spot market.
Another good example is the move to Bangladesh for cheap labor. In our work there we have watched uncontrolled pumping from the aquifer deepen the depth of water wells from 150 feet almost five years ago to 450 feet today. People have drilling rigs that are almost permanently attached to business parks. Access to water to dye the cotton is reaching a critical stage. Does cheap labor matter if you cannot access water to make the product?
There are other supply chain risks that are economic and social issues. Prior to my current work, I did a great deal of work around labor issues. I worked with large electronics companies, whose worker turnover rate in South China is over 80 percent a year. At what point in time do training costs and the quality impacts of so many new workers mean that it’s actually cheaper to pay your workers more?
A final example might be the integrity of the supply chain. Counterfeit parts for products in electronics and aviation are real issues for those businesses. They look like the real bolts and the real resins that you can buy, but they’re not. They are knock-offs, just like the fake Nike sneakers and Rolex watches. Companies have to do increasing amounts of physical and chemical testing on the parts coming in to make sure that they actually are as represented. These are substantial costs.
GT: How do you deal with issues like that?
PB: Think about how the sustainability risks you address can be expanded to help the company deal with the broader issues. There are a few basic steps companies can take to get a handle on these issues:
- Develop a relationship with your sourcing or supply chain person: People inside the business need to share information. A lot of times, sustainability people don’t talk to supply chain people; supply chain people don’t care about sustainability. It’s amazing how many times all they need to do is to get the people in the same room. Stakeholder conversations bring real value and real meaning when it comes to managing risks along the supply chain.
- Ask your suppliers: Instead of sending out so many audits, just ask them, “Do you plan for water risk?” Conversations are very good things because you find out things you can’t find out in a survey. In a checklist you only get what you ask. In a conversation, you have the opportunity to ask follow up questions.
- Map the supply chain: Businesses need to define the issues — the specific issues that apply to their products, operations and suppliers. A map can be geographic. But a process flow map of critical materials may well exist in your company right now. There is very likely a list of strategic or critical suppliers in your supply chain management team right now. What a great place to start adding value for your company. What are the sustainability risks of the suppliers on that list? Is there a water issue right now? What types of energy do they use? Is there an issue with labor access? People are frightened by the scope of their supply chain, which is why you start with something small, a map around a specific product, a specific process and then you focus on that.
- Prioritize the issues: Which are the areas with the greatest opportunity to reduce cost and risk? How do you prioritize which issues matter most? The conversation with your company’s supply chain professionals will help you understand what process they use to select critical parts or products — or select strategic suppliers. If you can understand their priorities then you can merge them with your existing priorities. It may not be perfect but it’s a place where you can get started.
PB: Yes! One of the factories we worked with in Bangladesh discovered that with an investment in water storage tanks and quality checks, they could begin to reuse their waste water in the production process. Today nearly 80% of their waste water is reused in production. This gave them multiple points to communicate to the western brands buying their products that: they had reduced their vulnerability to disruptions in water supply; they had demonstrated their innovation potential to their current customers; they had reduced their water use per unit of production; and they showed attentiveness to the needs of their current and potential customers. This work now takes a lead role in their efforts to secure orders from other western brands.
About the Author
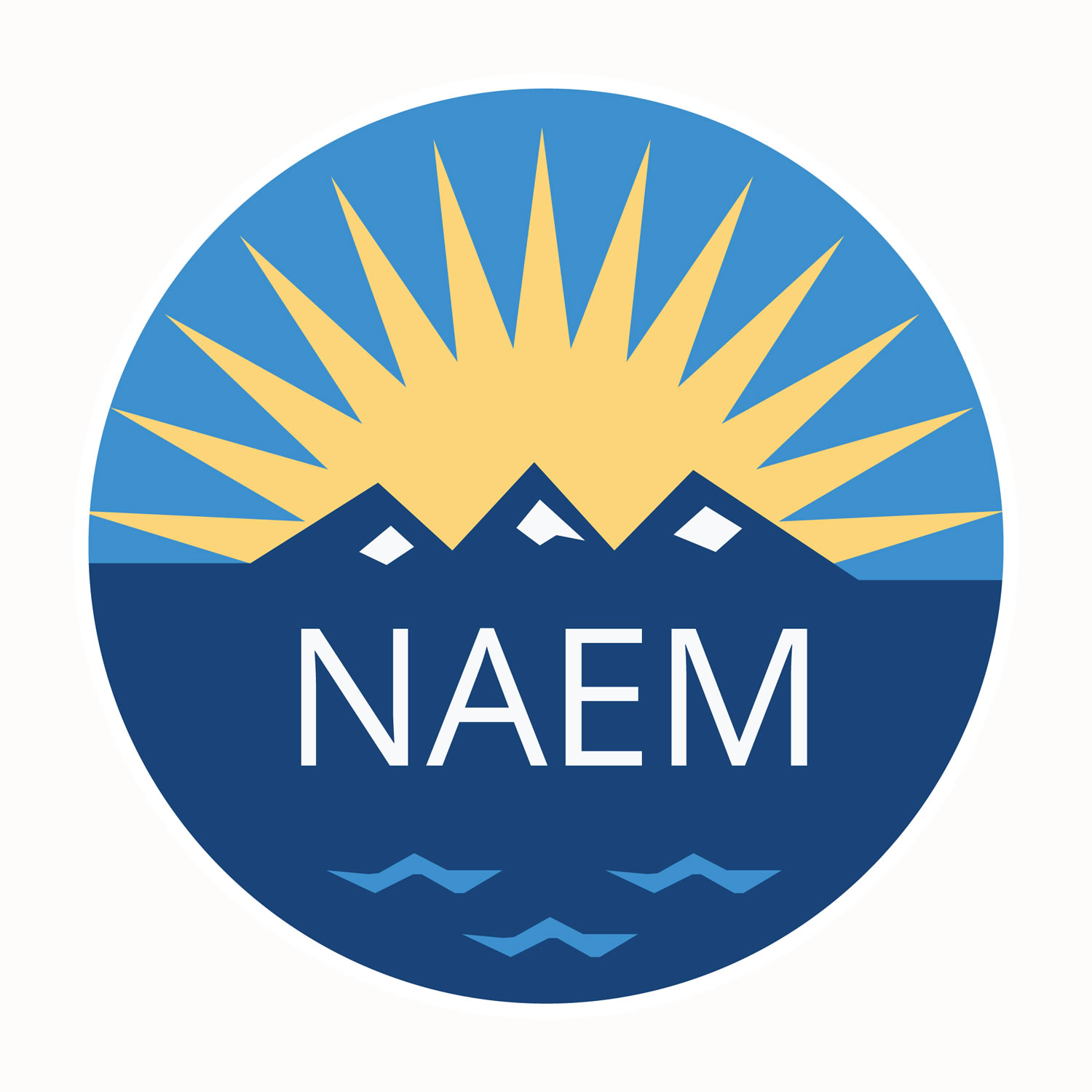
NAEM Staff
The National Association for Environmental, Health and Safety, and Sustainability (EHS&S) Management (NAEM) empowers corporate leaders to advance environmental stewardship, create safe and healthy workplaces and promote global sustainability. As the
leading business community for EHS&S decision-makers, we provide engaging forums, a curated network, peer benchmarking, research insights and tools for solving today’s corporate EHS&S management challenges. Visit us online at naem.org.