Using OSHA's Voluntary Protection Program to Advance Safety
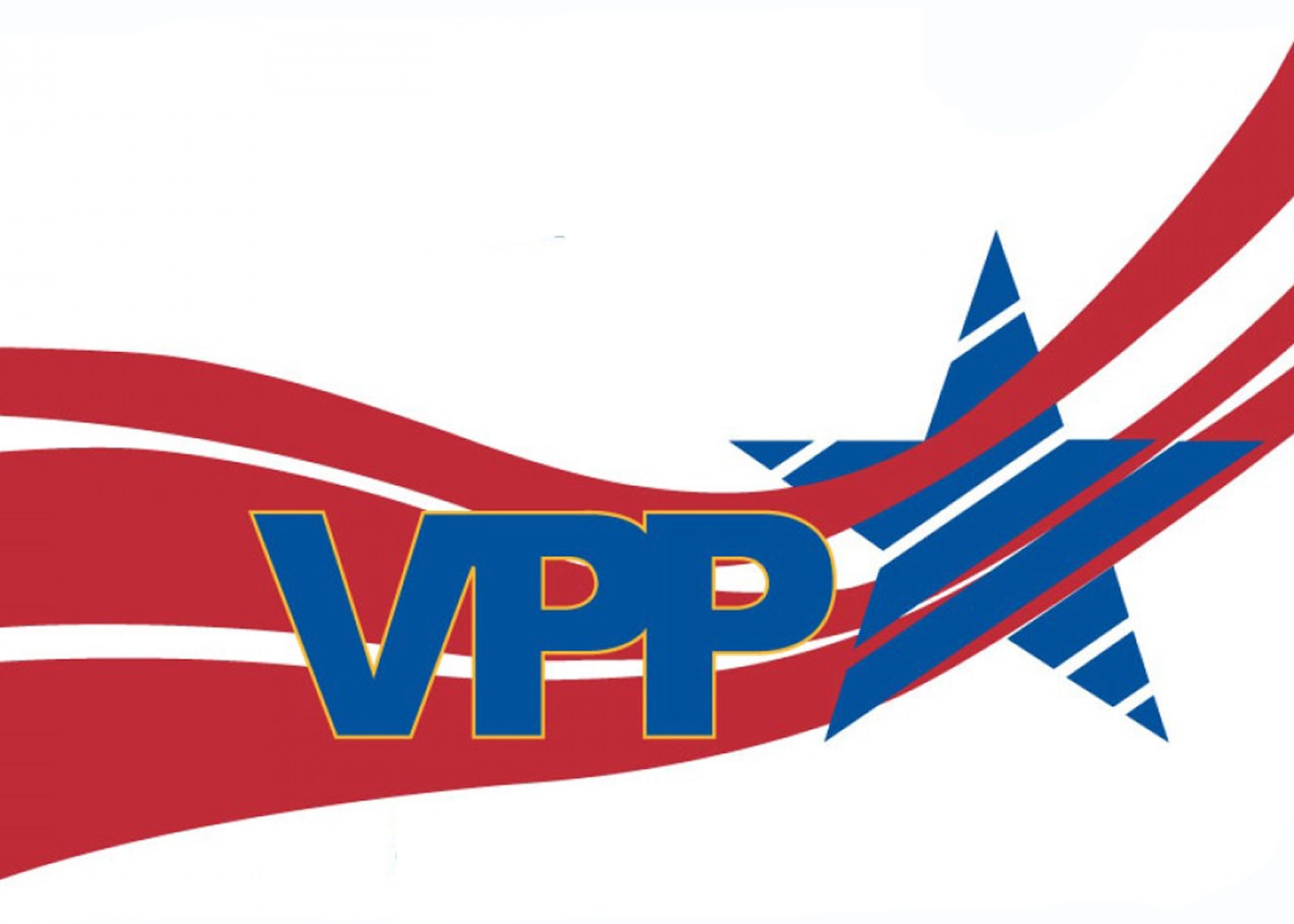
Q: What is VPP?
A: A program created by the Occupational Safety and Health Administration, VPP is a voluntary protection program, or a "best of the best" program in safety. There are four main elements to the program: Management leadership and employee involvement; worksite hazard analysis; hazard prevention and control; and safety and health training. They make sense because in order to have a comprehensive program in safety you need all of these elements. Both management and employees have to be on board, and the work site hazard analyses need to be done.
Q: How many workplaces participate in VPP?
A: There's approximately 9 million workplaces in the United States and there's only about 2400 or 2500 VPP-certified facilities. So it's a pretty high bar to achieve. The VPP program can either be run at the federal or the state level if the state has jurisdiction.
Q: How do you sign up for VPP?
A: Once you feel like you're moving beyond compliance (your OHSA requirement injury rate has to be less than or equal to the Bureau of Labor standards level), you have to put in an application to OSHA. You can apply on a site-by-site basis, or it can be done at the corporate level, but most folks do it on the site level, so your site itself has to be in compliance and it has to meet a rigorous set of requirements.
The comprehensive process takes anywhere from 6 to 18 months for a facility, depending on your safety level of maturity. You fill out an application, OSHA might come in to do a site visit to make sure you're ready, and then they actually come in and do an inspection of your facility. And the ultimate prize here is to become 'OSHA VPP-Star Certified'.
Q: How do you know you're VPP ready?
A: Everyone has to be totally engaged around safety in the facility. You have to review your facility on a quarterly basis, you have to do walk-arounds and look for any kind of unsafe behaviors or unsafe conditions. The leaders have to be talking about safety. You have to establish a formal safety committee and an active process for employees to bring issues forward. If there's a safety issue in their workplace, how do they get that resolved?
Q: How does the program work?
A: They have stringent requirements around things like subcontractors, for example. You have to have a really thorough program around your subcontractors and any associated risks. If you have an organized labor group on your facility, they have to actually sign a letter of commitment because OSHA knows that if you have a union on site and they're not in favor of this, the program will not be successful.
Once you're certified, the program involves best practice sharing among the other VPP companies. There's a mentoring aspect to it where you work with another company that's VPP-certified and then they ask you to do the same when you're certified, so you go out and help others. Regulatory VPP administrators also send out notes and questions that sites have relating to various safety challenges. Other VPP member companies respond in the spirit of benchmarking. It's really a spirit of cooperation, which encourages best practice sharing.
Q: What are some of the benefits of the program from your perspective?
A: It shows that your leaders are sincere about safety. It's a recognition that we're walking the talk, that we're putting our money where our mouth is. We're saying, "We're all about safety and we're willing to invest in it." So we're providing these tools, communicating openly, and we're going to act as a team to make our plant safer and more efficient. It also gives you a uniform platform for all of your safety programs and really helps get safety part of the company's DNA. Finally, it helps you grow professionally because it develops your safety programs and culture. It gives you exposure to all sorts of unique safety challenges and solutions from other VPP certified sites outside the company.
About the Author
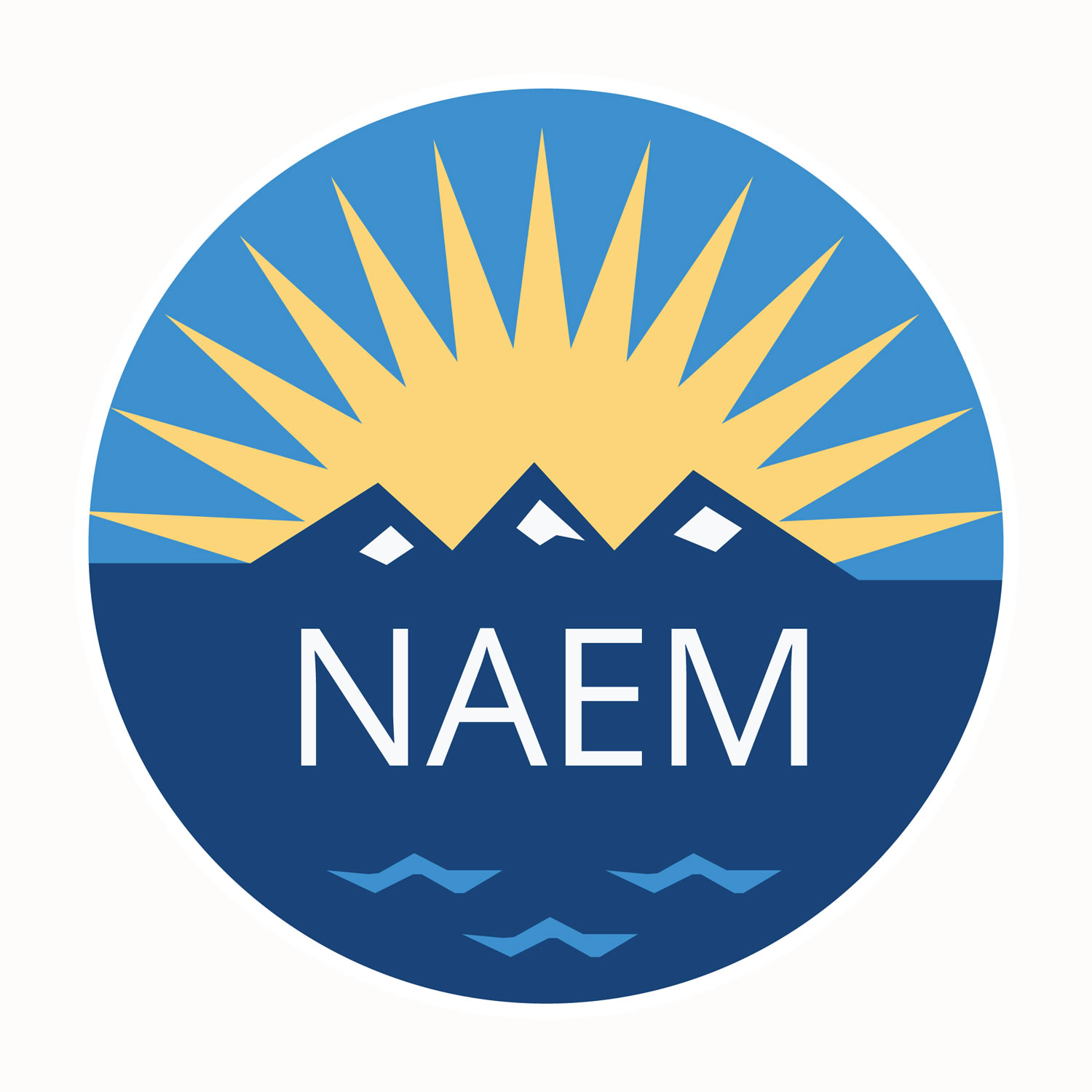
NAEM Staff
The National Association for Environmental, Health and Safety, and Sustainability (EHS&S) Management (NAEM) empowers corporate leaders to advance environmental stewardship, create safe and healthy workplaces and promote global sustainability. As the
leading business community for EHS&S decision-makers, we provide engaging forums, a curated network, peer benchmarking, research insights and tools for solving today’s corporate EHS&S management challenges. Visit us online at naem.org.