Alcatel-Lucent's Commitment to Supply Chain Safety
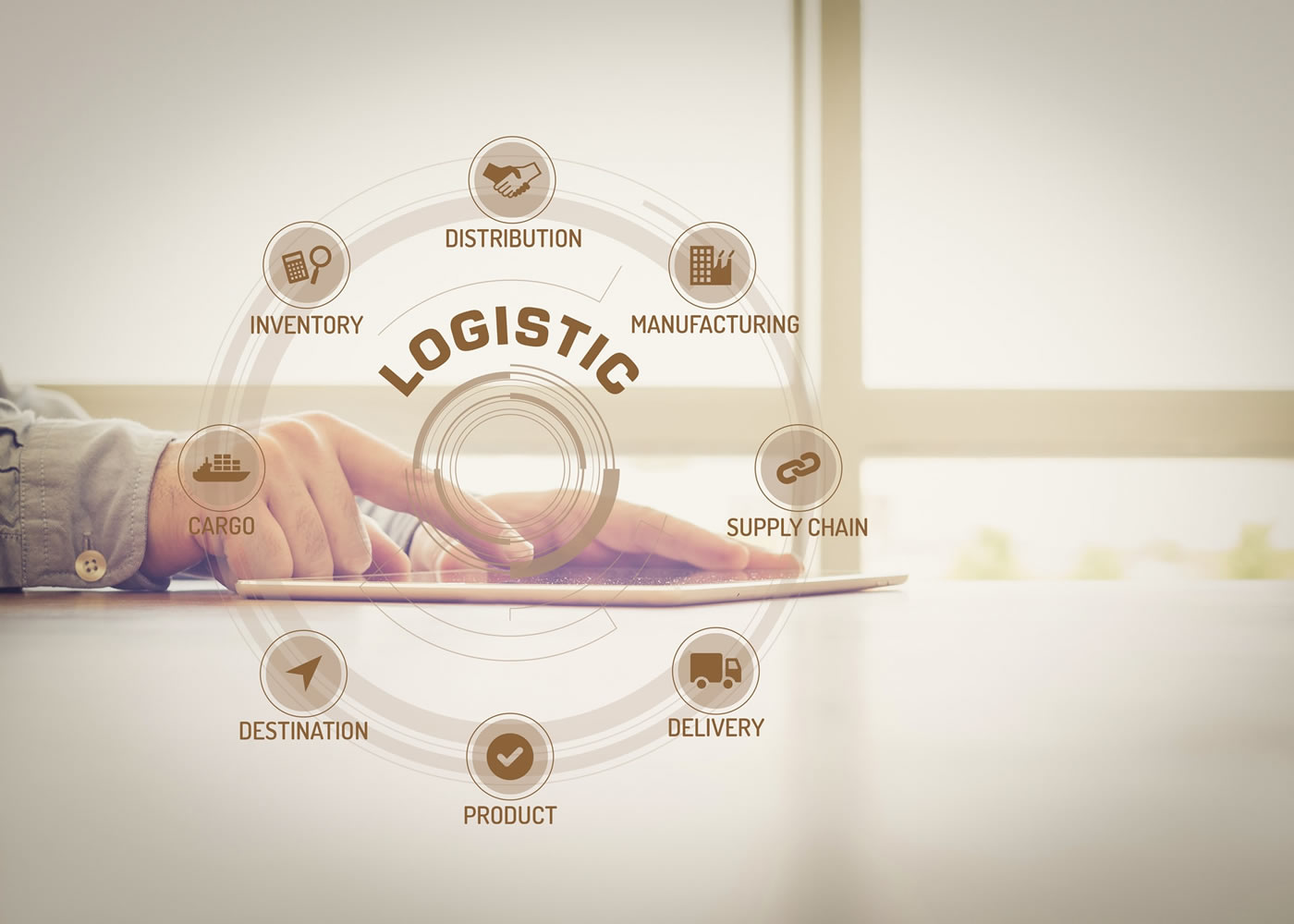
The Green Tie (GT): What are some of the biggest challenges for companies like Alcatel-Lucent when it comes to advancing sustainability?
Barry Dambach (BD): There's a whole element of sustainability that often gets overshadowed by other programs and that is safety. Many of us have this kind of environmental bend, where that's the angle we've been coming from. That's absolutely important but in all honesty, one of the most important elements is making sure everyone goes home safely at the end of the night. So that's a big focus that we're working on.
We're doing installation around the world in a lot of emerging markets, and a lot of our focus is in the safety risks associated with subcontractors on the installation side. We have people climbing cell towers, doing electrical work, and trenching to put fiber-optic cabling in. Another high risk area is the extensive driving of motor vehicles.
GT: You mentioned that you rely a lot on subcontractors for the installation work. Does that make it challenging to influence their safety performance?
BD: It's much easier to put programs in place, visually see what's going on, and work to continually improve the programs when you own the facility. When we're using third-parties it's much harder to determine if they have strong safety programs, especially when they are doing those high risk activities. I don't know if you've been to Brazil or India and seen the driving conditions. We would beg for the stop-and-go traffic on the beltway.
GT: So how do you ensure your employees remain focused on safety?
BD: A big piece is that we use a global EHS management system approach, structured on ISO 14000 and OHSAS 18000. We've also got global internal social media outlets that we use to communicate with our employees. We use third parties to track legal requirements around the world and then we communicate those with the local organizations and then my team provides subject matter expertise to help them implement ones that are applicable to them. We also use these shared platforms to communicate best practices such as a motorcycle safety driving program. We did not have experience of that in the U.S., but our folks in India had a program so we adapted that and made it available globally.
GT: How do you engage your subcontractors around the importance of safe practices?
BD: From a supplier standpoint, we're engaging directly with our subcontractors who are doing field work for us to make sure that they have programs to meet our global requirements. What you find is that many of these companies don't have any documented programs at all. We just went back and reviewed the programs from 800 subcontractors around the world doing high-risk activities for us. In cases where they're small companies that don't have large staff and limited capabilities to develop safety programs, we're doing mentoring programs with them. We're sharing some of our program elements with them so that they don't have to reinvent the wheel.
Our goal is to get them to a point where we're comfortable that they're implementing programs. We want to make sure that we've got a pool of subcontractors that can meet our needs when we have projects but who can also meet our needs from an EHS standpoint. It's a very different way of approaching the challenge but it's critical to us because once you make a commitment to only working with subcontractors that meet these standards, we have an obligation to help them get there.
About the Author
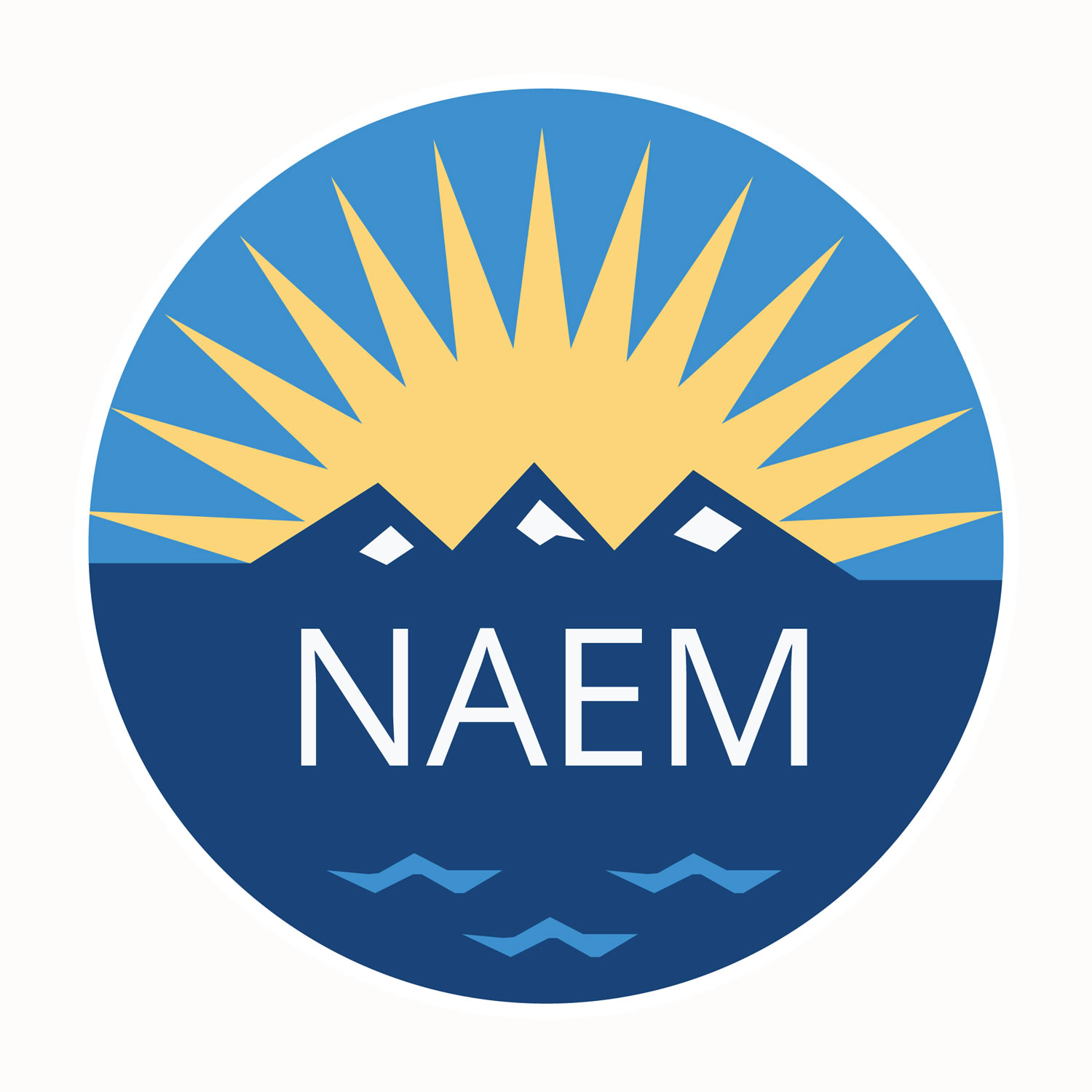
NAEM Staff
The National Association for Environmental, Health and Safety, and Sustainability (EHS&S) Management (NAEM) empowers corporate leaders to advance environmental stewardship, create safe and healthy workplaces and promote global sustainability. As the
leading business community for EHS&S decision-makers, we provide engaging forums, a curated network, peer benchmarking, research insights and tools for solving today’s corporate EHS&S management challenges. Visit us online at naem.org.