Fleet Safety Moves Into the Fast Lane
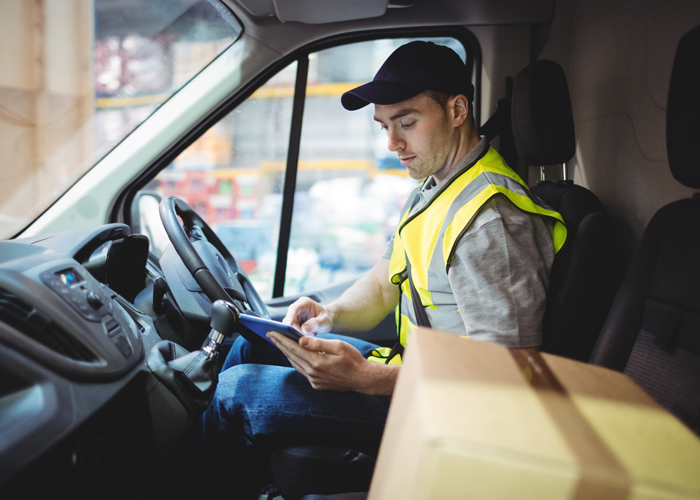
With more than 4,500 drivers out on the road delivering dairy products every day, Dean Foods is one of the largest distribution entities in the country. Michael Miller, Vice President of Environmental Health and Safety, says every incident or even near miss involving the company's fleet translates into real dollars and cents.
"Any vehicle accident could be a huge liability, whether or not it's our fault," he said. "[It] may be in a parking lot and they might sideswipe somebody's mirror or a car backed into our truck...Every single one of those incidents needs to be investigated; the drivers need to have a drug and alcohol test. So it's obviously very labor-intensive to manage all of those incidents."
For Frank Marino, Corporate EHS Manager for Raytheon, the key issue is the rise of cell phone use, which has heightened the risk of vehicle accidents among American drivers. According to research by the National Safety Council, drivers talking on cell phones are four times as likely to be involved in a car crash, regardless of whether they are using a 'hands-free' device.
As a first step toward addressing this issue, Mr. Marino has been holding a series of discussions with the Raytheon's leadership to present the latest research on the impact of distracted driving on employees' well-being with the goal of developing a policy to govern cell phone use while driving.
"Everyone says, 'No, I can [multi-task].' That's everyone's answer...but when you really look at the science of it, it's really not true," he said.
Indeed, research compiled by the NSC confirms that drivers talking on cell phones can miss up to 50 percent of their driving environment, including pedestrians and red lights, a phenomenon known as inattention blindness.
Making employees aware of these otherwise hidden risks of driving is part of the new, interactive training program that David Newman, Senior Director of Environment, Health and Safety, recently rolled out among the technicians at Comcast Cable.
"The old approach is that we have a defensive driving class," he said. "They have a ride and test at the end of it and then we would say, 'See you later for a couple of years.' But it wasn't working."
The new training program, on the other hand, is a completely virtual one, that asks employees to take a diagnostic test that measures their driving behaviors. Based on their performance, a 12-minute, targeted training module is emailed to the employee every month. Each module incorporates a mix of descriptive text, metrics and videos to accommodate a range of learning styles.
Mr. Newman said the convenience of the program allows employees to fit it in between jobs. For those who are constantly on the road, this alone is a cardinal advantage over a traditional classroom training environment. The other aspect that employees seem to like, he said, is the level of interactivity the program requires.
"When you're watching a video on there, or you're listening to someone talk with a video going, or you have to point and click on problems and you're taking a timed test so you only have 5 seconds to find it, you're very focused on what's going on," he said.
The program also engages employees with the company's policy regarding cell phone use.
"It reminds drivers about our distracted driving and hands-free policy at the beginning of the program, and then there are several test questions about that. So rather than signing off on an employee manual that's 100+ pages long, it's much more interactive and the employee realizes that we're really serious about that," he said.
The impact on drivers' performance so far has been impressive, he said. During the initial pilot with 500 drivers between 2013 and 2014, the company saw a 70 percent reduction in accidents that it hopes to achieve across its fleet of 30,000 vehicles. This was a statistically significant reduction in accidents, comparing both drivers who had been through the training and the drivers who hadn't, and also comparing the same drivers year-over-year, Mr. Newman said.
As he rolls this out to the full company, he said he expects the payback on the system will be a couple of months, just from having fewer accidents.
Mr. Miller at Dean Foods also recently introduced a new program to improve the overall safety performance of the company's fleet. The program uses a behavior-based safety model to engage employees.
"When you've got somebody out driving a truck and they're out on the road 10-12 hours a day and you only see them when they leave and when they come back, how do you coach them?
"It really ties into the behavior-based safety that a lot of people have done with employees in a factory so that now, you can do that behavioral safety with an employee that's out on their own," he said.
He began the process by piloting two leading telematics systems, which use dashboard-mounted cameras and computers connected to the engine to collect 18,000 data points about a driver's performance. Similar to an airplane's 'black box' technology, certain activities such as sharp turns, bumps, braking and fast acceleration trigger a 'recording event'. Those recordings are then reviewed by a central call center which decides whether to pass the information along the company's supervisors for further review.
"Our supervisors are now interacting with our drivers on a weekly basis, because our supervisors are now having to conduct coaching sessions and the coaching sessions require them to sit down with our drivers," Mr. Miller said.
The feedback conversation that comes results from this process was as important to the company as the goal of reducing the overall risk and liability, he said.
"We view it as game footage...This tool was not designed to be a discipline tool; it's a tool to increase the skill set of our drivers and to help them improve."
The company is now in the process of running a 14-month pilot among two divisions, with the aim of installing cameras in all trucks by December 2016. Based on its benchmarking with other companies using the same system, the break-even cost for the fleet may be a 25 percent reduction in accidents, while the average company achieves an accident rate reduction of 50 percent.
To help ensure its success, Mr. Miller's team has dedicated more than six months to explaining the benefits of the program to the drivers themselves, a strategy that seems to be working.
"They're enthusiastic that they have a tool that can defend them or explain when they get into an accident," he said. "It's important to note that the behaviors that are observed are not only negative. We're going to be observing positive behaviors, too."
Related
Sponsored Content
About the Author
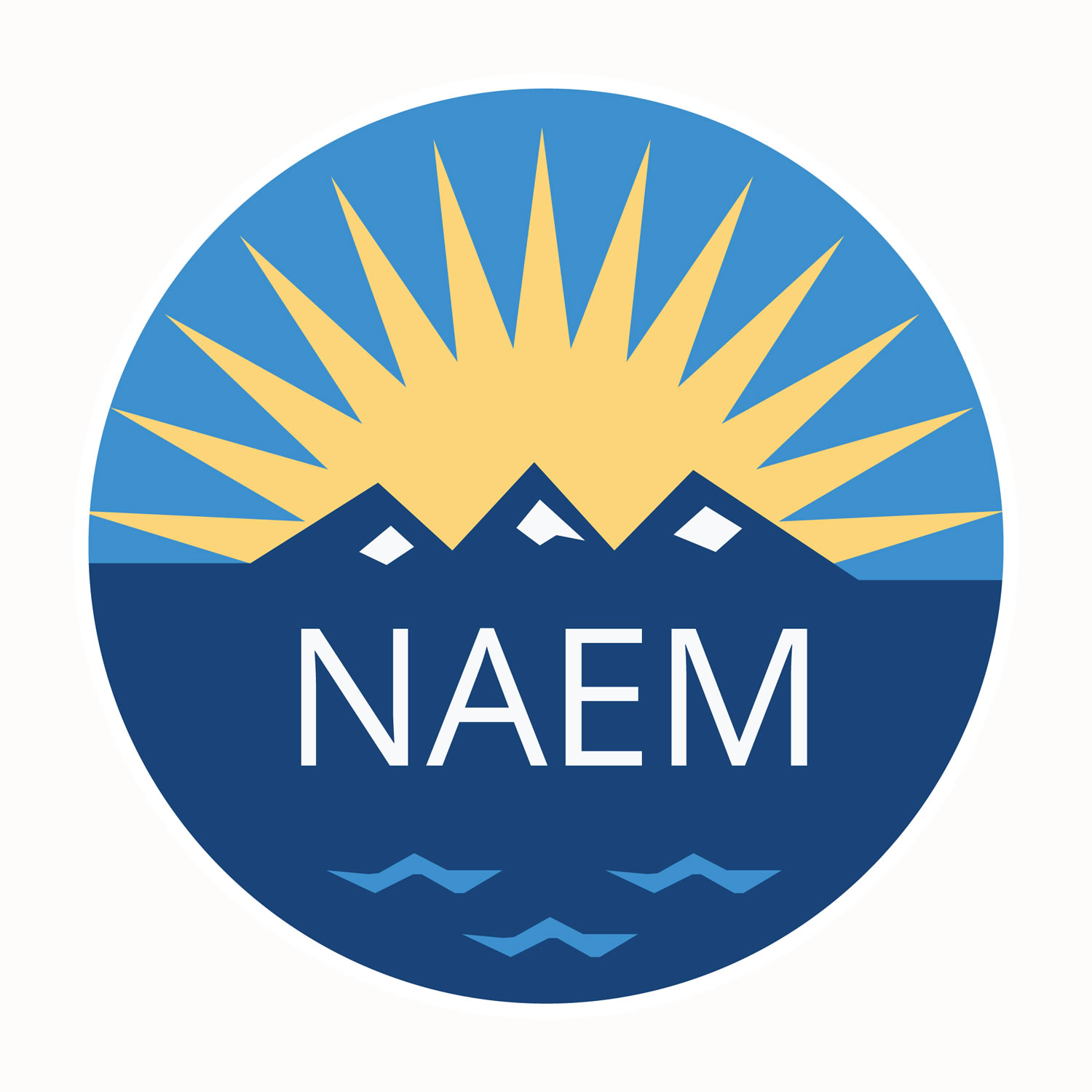
NAEM Staff
The National Association for Environmental, Health and Safety, and Sustainability (EHS&S) Management (NAEM) empowers corporate leaders to advance environmental stewardship, create safe and healthy workplaces and promote global sustainability. As the
leading business community for EHS&S decision-makers, we provide engaging forums, a curated network, peer benchmarking, research insights and tools for solving today’s corporate EHS&S management challenges. Visit us online at naem.org.