4 Keys to a Solid Safety Audit and Inspection Program
Sponsored by: KPA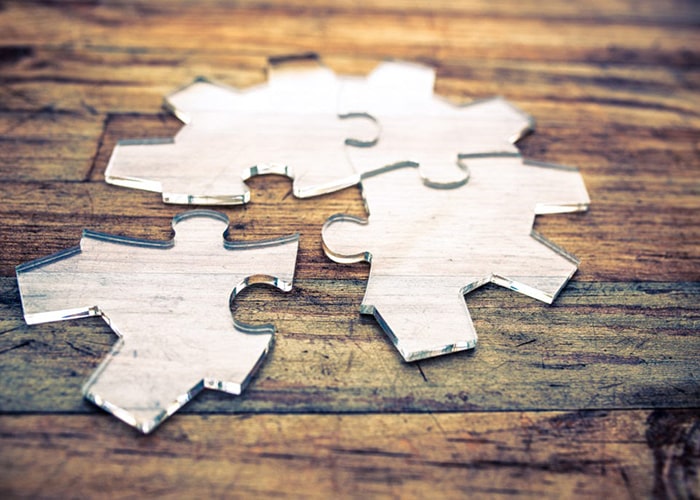
You'll also minimize your regulatory and legal risks. Audits and inspections ensure you stay 10 steps ahead of the Occupational Health and Safety Administration, the Environmental Protection Agency, and the other federal and state authorities just waiting to hit you with citations and penalties.
If you find the prospect of audits and inspections overwhelming, you're not alone. After all, there's a reason organizations don't conduct them as often as they should. So let's make this as simple and painless as possible by breaking audits and inspections down into manageable pieces. These are the 4 basic components that, when combined, form a comprehensive assessment of your EHS program.
Part 1: The Regulatory Audit
What it covers:- OSHA compliance
- EPA compliance
- DOT compliance
- NFPA compliance
- compliance with state and local regulatory requirements

Examples of questions an auditor should ask:
- Are all employees trained properly?
- What are your safety policies, and are employees actually following them?
- Is any written compliance program in place?
- Have you conducted a hazard assessment?
- What is the condition of personal protective equipment?
- What are your chemical storage procedures?
- Do you have all required hazardous materials paperwork?
- What are your machine guarding (AKA Lockout/Tagout) procedures?
- What are your respiratory protection procedures?
- Are any fall hazards present in the workplace?
- What are your shipping, warehousing, and transportation procedures?
- Are sprinkler systems in good working order?
- Is all necessary safety signage in place?
Part 2: The Facility Inspection
What it covers:- department-specific regulatory compliance
- department-specific safety hazards
- equipment and machinery
- documents
- employee behaviors

Examples of questions an auditor should ask:
- What is the layout of your facilities?
- Are your ladders in good condition?
- How about your forklifts?
- Have you tested your alarms recently?
- Where are your eyewash stations?
- How about your fire extinguishers?
- What's the condition of walking and working surfaces?
- Does anything require maintenance?
- Are employees trained to use the tools they're using, and are they using their tools safely?
- How are employees performing their jobs?
- Do employees have any feedback about how to improve the EHS program?
Part 3: Accident Investigation
What it covers:- workplace accidents
- employee injuries
- incident response
- preventive measures
- corrective measures
- workplace safety trends

Examples of questions an auditor should ask:
- How many safety accidents have occurred recently?
- What is the nature of those accidents?
- What are your accident response procedures?
- Which employee or employees are responsible for gathering the details, documenting accidents, and following up?
- Is there a standard, repeatable accident response process in place?
- Are accidents addressed and documented in a timely manner?
- Why are accidents happening? What are the root causes?
- What kinds of accidents occur most often?
- What are the costs of accidents in the workplace?
- What can be done to prevent accidents in the future? What organizational practices and operating procedures need to change?
Part 4: Safety Committee Meetings
What they cover:- Overall EHS program function and effectiveness
- EHS program efficiency
- Safety team roles and responsibilities
- Current priorities and improvements to make
- Timetables for implementing changes
- EHS program budget and costs

Examples of questions safety committees should consider:
- Are all employees working as safely and efficiently as possible?
- Are all members of the organization, including leadership, engaged and represented in EHS program decisions?
- What safety and regulatory risks does the organization currently face?
- What aspects of the organization's EHS program are functioning as intended?
- Are there any gaps in the program?
- What needs to be improved?
- How soon will changes be made?
- What are the costs of improvements?
- What is the ROI of an optimized safety program?
- Who is responsible for coordinating EHS program changes?
- What will the schedule be for inspections and audits moving forward?
We'll level with you—audits and inspections can be a lot of work.
But they're easier, cheaper, and a whole lot less stressful than dealing with accidents, losses, penalties, legal claims, workforce turnover, and the myriad other adverse consequences of a poor EHS program.Effective audits and inspections not only save lives, but also tend to...
- lower workers' compensation costs,
- prevent citations and fines,
and - boost workforce productivity and retention.
Fortunately, you don't have to do any of this alone. KPA's workplace safety experts are available on-demand—on-site or remotely—to conduct audits and inspections, or guide you through the process. Contact an expert.
Audit and Inspection Tools in Vera Suite

Vera Suite users have the power to create inspection templates, customize existing EHS compliance templates, and assign inspections to individual users for completion.
Inspections can be tailored to the specific needs of your facility, making it even easier to remain compliant with OSHA workplace safety regulations. By streamlining inspection processes , you'll quickly uncover issues and address them with corrective and preventative actions before an incident occurs.
Discover how KPA's all-in-one EHS and workforce compliance software platform keeps your people safe, saves you time and money, and empowers you to proactively control your risk. Get a demo.
About the Author
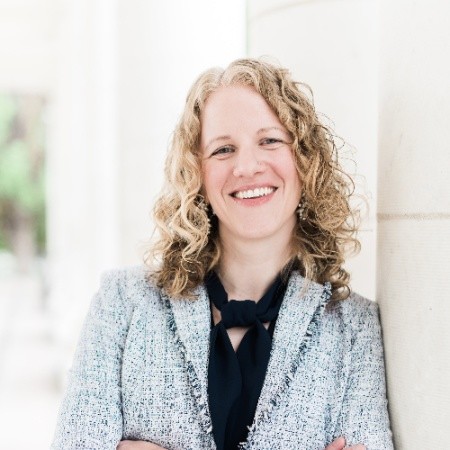
Jill Schaefer
KPA
Jill has 20 years of communications experience, ranging from PR to marketing and leadership. She’s a writer at heart who has spent her career teaching and storytelling on important topics like safety, compliance, energy efficiency, healthcare, and education. Words, powerful graphics, and creativity motivate her.