Building the Case for EHS Software: How to Gather the Data You Need
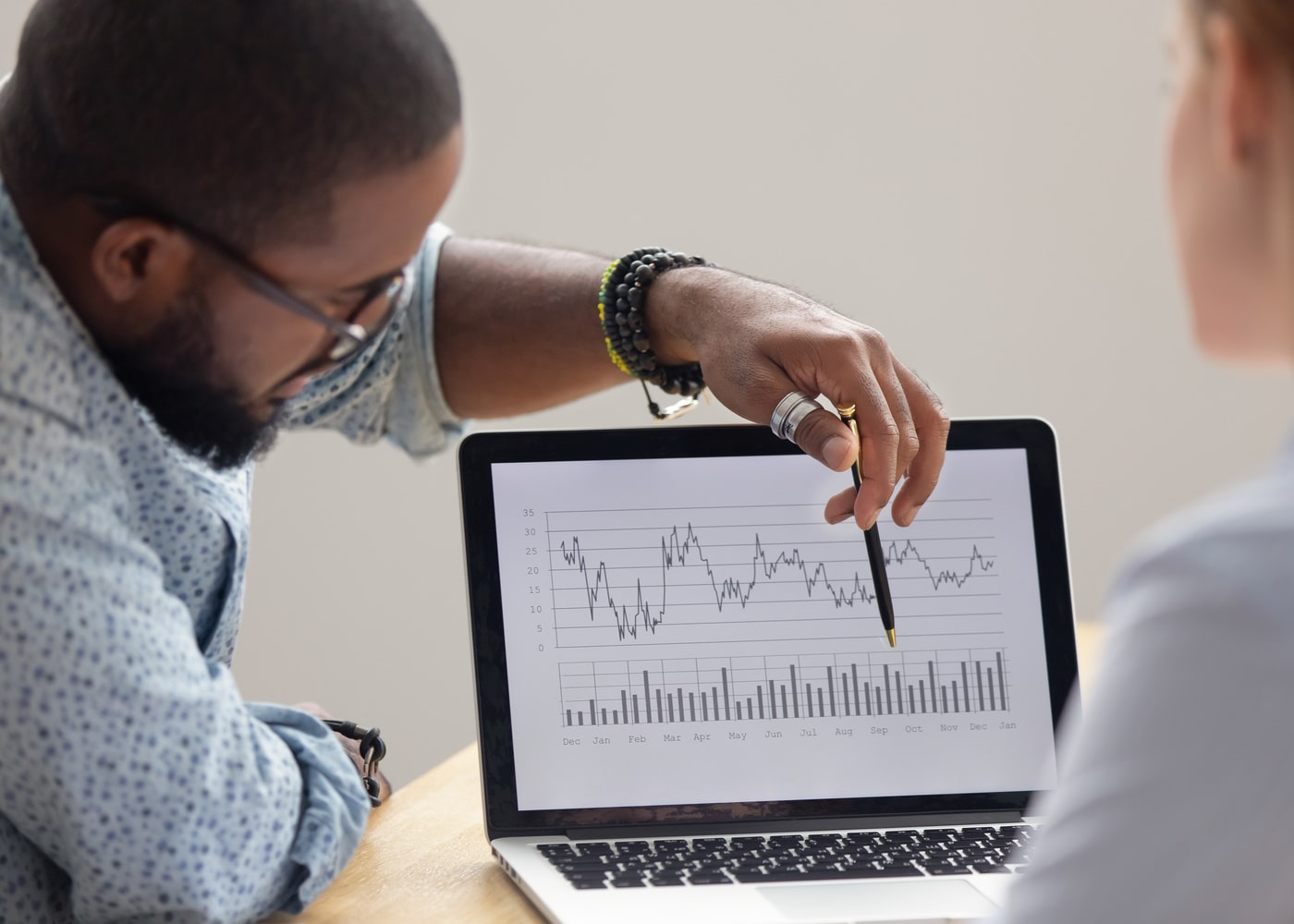
However, convincing decision-makers to invest in EHS software requires a solid business case backed by reliable data. This article will guide you through the data gathering process to create a compelling case for adopting EHS software.
Gather the Data You Need
EHS software is vital for organizations seeking to improve their health and safety culture in the workplace, reduce environmental risks, and streamline compliance efforts. When properly implemented, it can lead to significant cost savings and operational efficiency - in addition supporting a strong, transparent safety culture.Unfortunately, few employers have an enterprise-wide EHS system of record. Among large employers, analysis by Verdantix found that many firms use a half dozen, or more, software products to manage various EHS functions. Alongside that, roughly 1 in 3 US employers relies fully on outdated manual processes for recording incidents, tracking corrective and preventive actions (CAPAs), and conducting audits and inspections. If you are in one of these predicaments, here are steps that may help you convince leadership to digitally transform your EHS program:
Identify Key Performance Indicators (KPIs)
The first step in building a business case is selecting relevant KPIs, which are quantifiable measures used to evaluate the effectiveness of your organization's EHS efforts. EHS KPIs to consider include:- Incident rates: Number of workplace incidents per hours worked
- Lost-time injury rates: Number of lost-time injuries per hours worked
- Total recordable injury rates: Total injuries and illnesses per hours worked
- Environmental compliance: Frequency and severity of environmental non-compliances, such as emissions or waste disposal violations
- Training completions: The percentage of employees who have completed health and safety training applicable to their roles
- Training effectiveness: Employee understanding and application of safety and environmental protocols. To achieve this, you can use surveys, quizzes, and assessments to test their knowledge of what they have learned. You can also observe their behavior in the work environment and evaluate their compliance
- On-time action item closure: The percentage of corrective and preventive actions completed according to schedule is a leading indicator tightly linked to reductions in workplace incidences and injuries
Collect Historical Data
Historical data is crucial for identifying trends and establishing a baseline to measure the potential impact of EHS software. Begin by reviewing existing records, such as:- Injury and illness reports: This data helps to understand the frequency, severity, and causes of workplace incidents
- Inspection and audit findings: Reviewing past inspection results can reveal patterns and areas of concern
- Regulatory compliance documentation: Analyzing compliance records can uncover instances of non-compliance and their consequences
Benchmark Against Peers or Industry Standards
Benchmarking involves comparing your organization's performance with industry standards to evaluate how you fare against competitors. This practice can be a powerful tool for identifying gaps and opportunities for improvement. For example, a construction company can compare its lost-time injury rates to construction industry benchmarks to gauge the effectiveness of its health and workplace safety programs.To find industry standards or peer averages, there are various methods available. One excellent starting point is to compare your organization's numbers with industry benchmarks. The Bureau of Labor Statistics provides a helpful chart of incidence rates of nonfatal occupational injuries and illnesses by industry and case types that can be used for this purpose. By referencing this chart, you can clearly understand how your organization's safety and health performance compares to industry standards.
You can also engage software providers to help you document the differences between a high performing peer and middling or lagging competitors. Contact our team if you’d like to review how your organization stacks up against similar companies on several EHS metrics. One of our EHS experts can also identify the software modules that are most directly linked to performance improvements, allowing you to start your digital transformation on the right foot and expand into additional modules when your business is ready.
Quantify the Anticipated Benefits
Next, estimate the potential benefits of implementing EHS software, both financial and non-financial. These include:Cost savings
- Reduced incident rates: Fewer incidents can lower workers' compensation costs and lost productivity
- Lower workers' compensation costs: Enhanced health and workplace safety measures can lead to reduced insurance premiums
- Decreased regulatory fines and penalties: Improved compliance can minimize the risk of fines and legal action
Productivity Improvements
- Improved employee morale: A safer work environment can lead to higher job satisfaction and reduced turnover
- Streamlined processes: EHS software can help automate reporting, auditing, and training, leading to increased operational efficiency
- Faster closure of action items: task owner notifications and improved visibility into open action items can prevent costly delays to CAPAs
Revenue Gains
- Enhanced reputation: Demonstrating a commitment to safety and environmental stewardship can improve your company's reputation among customers, investors, and regulators
Conduct a Return on Investment (ROI) Analysis
To make a persuasive business case, conduct an ROI analysis to demonstrate the potential financial benefits of EHS software. This analysis involves estimating the cost savings (from reduced incidents, lower workers' compensation costs, and decreased fines) and comparing them to the implementation and subscription costs of the software. Ensure the projected ROI aligns with organizational goals and incorporates data regarding your organization’s current state wherever possible.The team at ProcessMAP, an Ideagen solution can offer an outside perspective on conducting this analysis, including metrics to include, methods of obtaining current state data, and peer benchmarks.
Present Your Case
Organize the data collected clearly and concisely, using visual aids like graphs and charts to display trends and contrast the current state with the results your organization can produce with better tools. Do not rely fully on data to present the argument, however. Tell a story about the impact on workers, to underscore that safety improvements are not simply metrics - they are fewer injuries, fewer absences, and fewer impacted workers and families.Anticipate the types of objections and questions you may receive and prepare answers for them. Questions about evidence that a software provider delivers on its promises, for instance. Or skepticism that front-line workers will use an EHS mobile app or kiosk application. You may also hear concerns about the ability to sync data between multiple internal systems required to provide a full picture of EHS risks and performance.
Finally, link the investment in EHS software to your organization’s mission, values, and strategic goals. Describe how a better EHS system of record will strengthen your organization’s safety culture.
Don’t Go It Alone
Digitally transforming your EHS program can be a game-changer for safety performance and safety culture. Yet, convincing leadership to invest in EHS software capable of providing enterprise-wide visibility, automation, and access can be a daunting task.Not sure where to start, or need help building your case? Click here to schedule a consultation with one of our experts and discover how we can support your efforts.
Related
Sponsored Content
About the Author
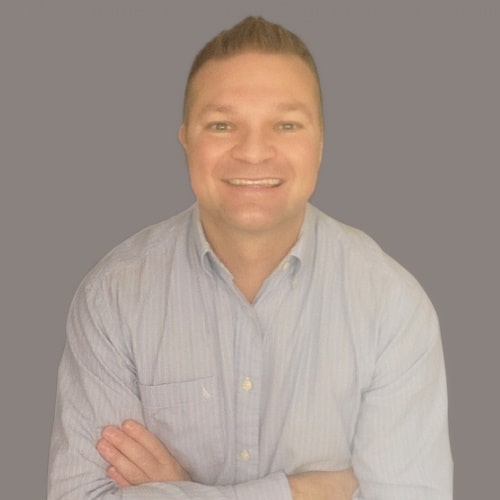
Jeramy Hurt
ProcessMAP, an Ideagen solution
At Ideagen, Jeramy helps employers determine the best technology strategy for automating their EHS processes and define the requirements for achieving that strategy. Jeramy brings 18 years of experience, including senior EHS roles at PepsiCo, Valvoline,
ABB, PPG, and Del Monte. Jeramy has a degree from Indiana State University, is a member of the American Society of Safety Professionals and is a Certified Safety Professional through the BCSP.