PFAS Tipping Point: Minnesota Passes Strictest PFAS Ban to Date
Sponsored by: Assent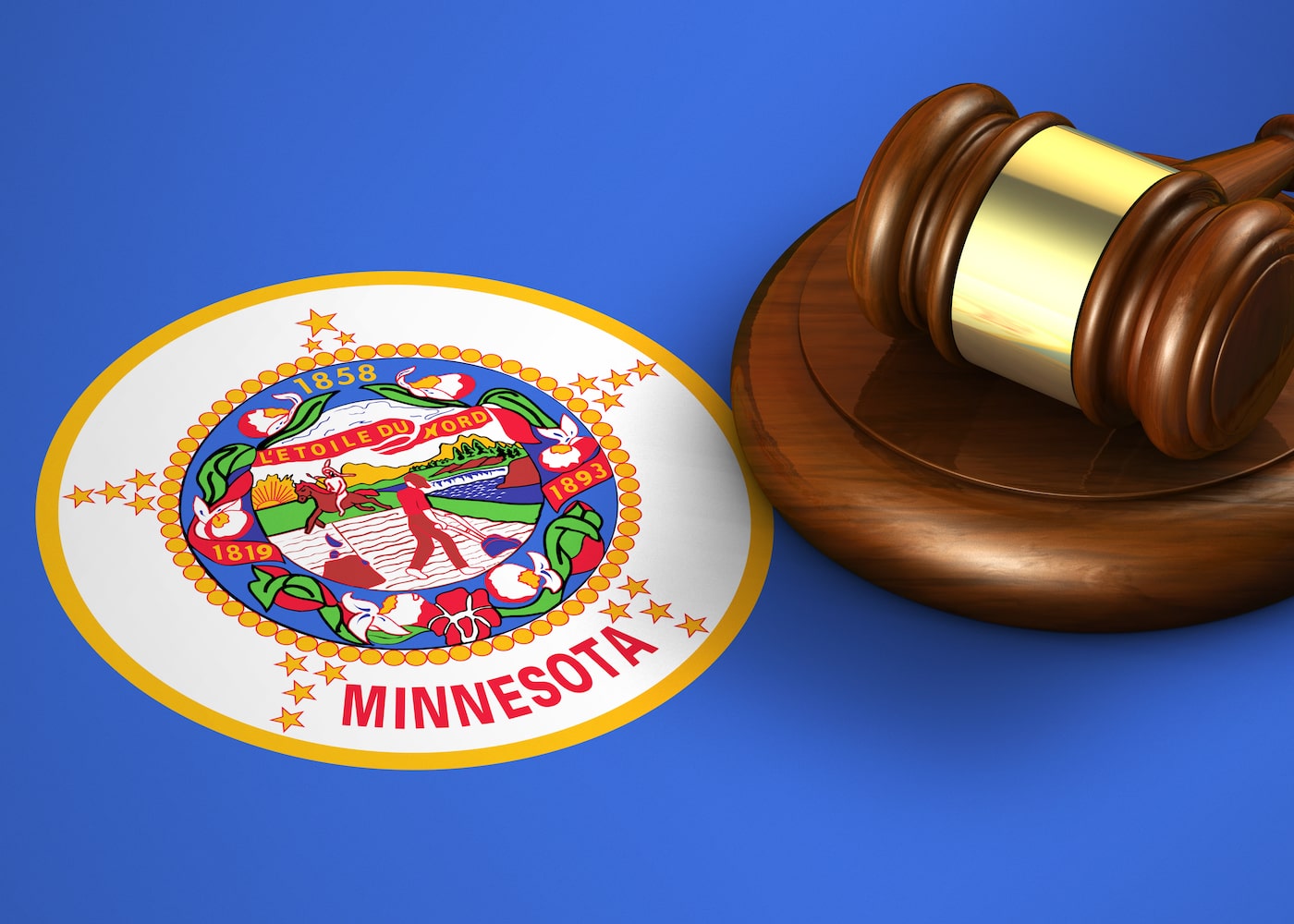
PFAS restrictions in the U.S. have reached a tipping point, with Minnesota surpassing Maine with the broadest PFAS ban to date on May 24, 2023. These PFAS requirements will cause reporting, restrictions, outright bans, and even product obsolescence for certain parts used in processes or trigger the need to re-engineer product formulas.
This means it is vital that manufacturers understand where PFAS are used in their production processes and products and that they establish a strategy for usage reporting at both state and federal levels. They also need to understand if emerging sales bans on certain types of products will directly impact them by restricting their market access, or indirectly if they use these materials for their own manufacturing operations. Finally, they need to be prepared for the “all products” PFAS sales restrictions that will go into effect in multiple jurisdictions in the next five to ten years.
Minnesota's PFAS Ban Sets a Sky-High Precedent
In late May, Minnesota Governor Tim Walz signed a new environmental budget bill into law that includes broad new PFAS requirements. In doing so, he set a deadline for product-level PFAS reporting, restricted the use of PFAS in 11 different product groups, and created an eventual blanket ban on all non-essential uses.Many analysts are calling this the broadest state PFAS law in the nation, restricting a larger group of products than any other state. The new bill:
- Prohibits the sale of certain products containing PFAS by 2025, including class B firefighting foam, carpets and rugs, cleaning products, cookware, cosmetics, dental floss, fabric treatments, juvenile products, menstruation products, textile furnishings,
ski wax, and upholstered furniture.
- Requires reporting for all products sold in the state that contain PFAS, taking effect in 2026.
- Prohibits all products with PFAS from being sold in the state by 2032, unless that use is essential for public health.
Manufacturers should also evaluate the products they use in their plants — including machine maintenance and personal protective equipment (PPE) — to ensure they aren't dependent on materials that will be phased out in the coming years. 3M announced it was discontinuing PFAS productionby 2025, meaning many products will become obsolete well before the 2032 ban. Early supply chain obsolescence for critical materials may be even more impactful for business continuity than the regulations themselves.
Maine Lawmakers Turn Sights on Supply Chain Data
Maine's PFAS restriction and reporting rule took effect in January 2023, but the database required for reporting and fee payment is not yet ready. The state Department of Environmental Protection (DEP) gave hundreds of companies an "extension" on the requirement to report all products being sold that contain PFAS. Numerous amendments were proposed to adjust this rule, leading some manufacturers to predict that they would effectively kill or significantly modify the law. However, four of the five died in committee.In early June, the governor signed one of these amendments — LD217 — into law. Most significantly, the amendment will push back the mandatory reporting date from January 2023 to January 2025 (retroactively). It also includes a small business exemption for businesses with 25 or fewer employees and clarifies some of the packaging reporting requirements. However, it does not eliminate the 2030 PFAS “all but essential products” ban. LD 217 also allows PFAS amounts to be reported based on information provided by a supplier rather than testing. The original rule required testing data against the Environmental Protection Agency (EPA) CompTox list of 12,000+ PFAS. However, this would be difficult, if not impossible, as test methodologies haven't yet been developed for the majority of PFAS.
Collecting Supplier Data for PFAS: Best Practices
When it comes to PFAS reporting and compliance, the following best practices will help manufacturers get ahead of their requirements:- Use supply chain data for PFAS reporting instead of testing methods.
- Supply chain data is more cost-effective and readily available.
- Supplier data is already used to comply with other composition regulations like RoHS and REACH.
- Even the EPA, in their proposal for PFAS reporting under TSCA Section 8(a)(7), refers to collecting data from supply chains for reporting.
- Supply chain data is more cost-effective and readily available.
- Engage suppliers early to collect information about PFAS presence in purchased materials.
- Utilize the list of active PFAS in the TSCA Inventory for data collection.
- Take the data you collect based on the TSCA Inventory and use it to comply with individual U.S. state regulations.
- Utilize the list of active PFAS in the TSCA Inventory for data collection.
- Provide additional support and education to suppliers from areas with fewer PFAS restrictions.
About the Author
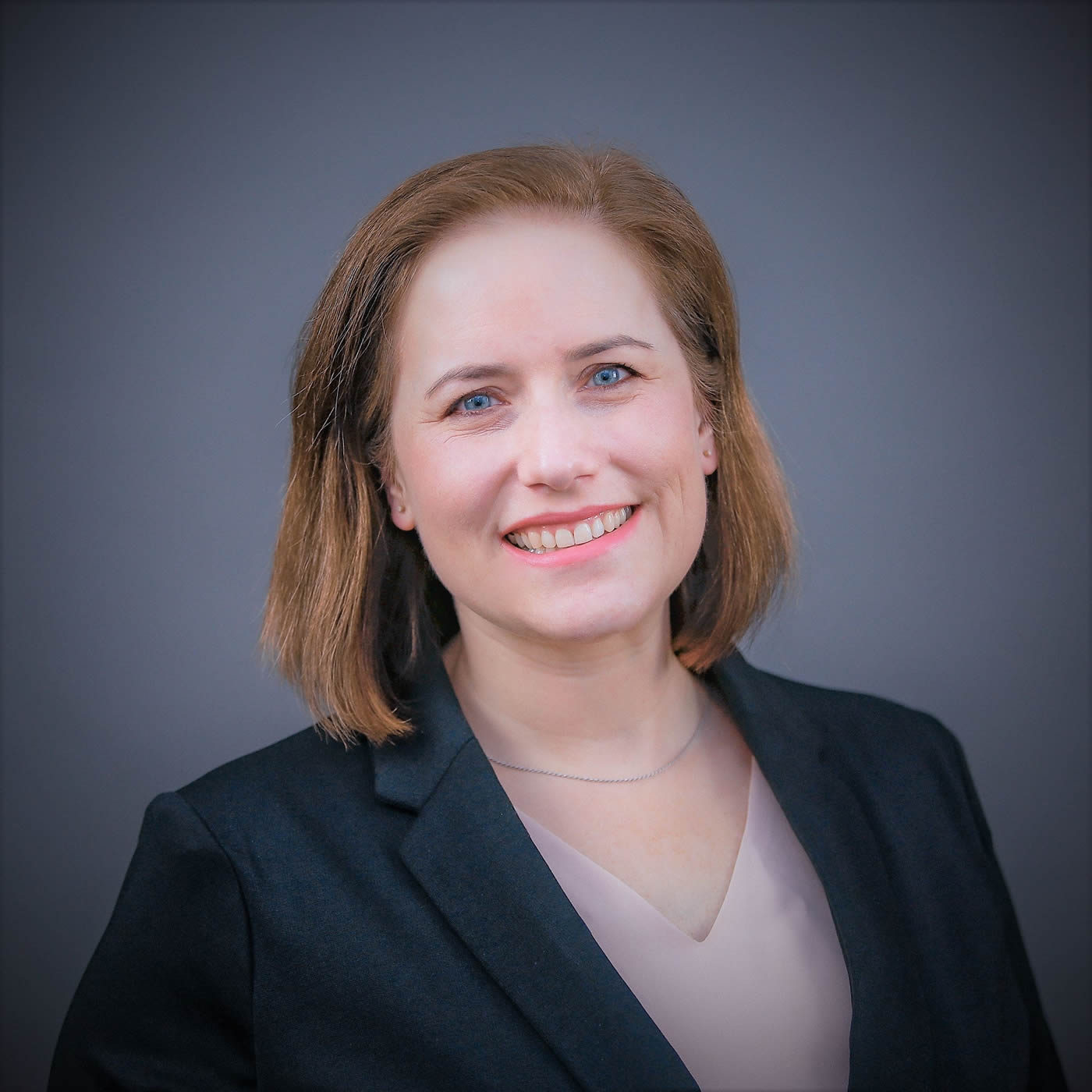
Cally Edgren
Assent
Cally is a proven compliance program leader with experience developing, communicating, and executing company goals and strategies. She is a subject matter expert on product materials compliance as well as market access certifications and has a background
in program and process development to support regulatory compliance requirements. Cally possesses over 27 years of experience in developing and managing global compliance programs at Rockwell Automation and Kohler Co.